Chaku Chaku is a way to operate a semi-automated manufacturing line. One (or more) workers walk around the line, add parts to the processes, and then start the process. While the process works on the part automatically, the worker adds the next part to the next process, and so on.
Efficiency
Line Layout Strategies – Part 2: I-, U-, S-, and L-Lines
The layout of a line can make quite a difference in the performance of your line. The U-line is most famous, although in my view while good it may not be the right thing for all situations. There is also the I-line, the S-line, and the U-line. In my last post I described some general thoughts on line design and took a look at the big picture. In this post I want to look at and compare actual line layouts, in particularly the I, U, S, and L layout. Let me give you an overview of the different options.
Line Layout Strategies – Part 1: The Big Picture
In flow shops, you have a production line of some sort. This may be an assembly line or a manufacturing line; this may be automatic or manual. In lean, you often hear about the famous U-line.
While this is a great solution, it may not fit all problems. Depending on the surrounding conditions, a different line layout may be beneficial. This post is the first in a series on line layout. In this post I would like to discuss what you should consider when designing a new line layout. The next post will look at actual line layout options.
Toyota’s and Denso’s Relentless Quest for Lot Size One
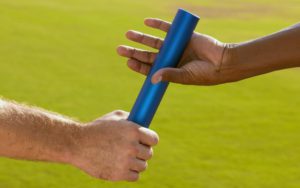
A famous step toward perfection in a lean production system is a lot size of one. However, few people realize what enormous effort and rigor Toyota applies to achieve this goal. During my visit to a Toyota plant and the APMS conference in Tokyo in 2015, I saw quite a few stunning examples of this quest. Let me show you …
Tales from Japan – Lean in the Japanese Public Toilet
Whenever I am in Japan, I look for examples of lean behavior visible to the public (see, for example, Japanese Standard Pointing and Calling). This time I would like to talk about Japanese public toilets and all the nifty features to make their use a pleasant experience. You will be surprised how much thought goes into public toilets in Japan. The same level of attention to detail is also something necessary for good lean implementations. Japanese public toilets in particular do a great job servicing the not-average user!
Lean for Refugees
Europe is currently experiencing a refugee crisis. Hard numbers are difficult to obtain, but it is estimated that one million refugees arrived in Germany in 2015. Government authorities were ill-prepared to handle and organize these people. Significant resources have been put in, but they never seem to be enough. The organizational processes are not yet functioning well.
As it happens, I am an expert in improving organizational and other processes. I decided to help, and together with two other professors, founded an initiative, Lean for Refugees. We are politically neutral, volunteering our time to organize these processes so we can help both the refugees and the government. Let me give you an overview of what we have done so far.
How to Reduce Your Inventory
Reducing inventory is one of the goals of lean manufacturing. In my last post I described why we need inventory in the first place, and why too much inventory is bad for you. Now let’s look at how we can achieve a good inventory level. First, an important statement: Inventory is not a lever that you can pull. It is more the result of other good lean improvements. In fact, merely pulling this lever and reducing inventory will actually make things worse. To gain the true benefits of lower inventory, other measures have to be taken. In this post I would like to describe what happens if you simply reduce inventory, and how to do it to achieve a lower inventory without causing mayhem in the process.