SMED (Single Minute Exchange of Die) is a very useful tool to reduce changeover time. Reducing changeover time will free up time for other uses. Western management often wants to use this time to produce more goods. However, the rule of thumb at Toyota is to use this newly available time to do more changeovers rather than more products. This increase in changeover has the potential to significantly reduce the lot size, which often has much larger benefits than the additional work time. In this blog post I want to look in more detail at this relation between changeover duration, productivity, and lot size.
Inventory
Loss of Material: Theft!
Toyota’s and Denso’s Relentless Quest for Lot Size One
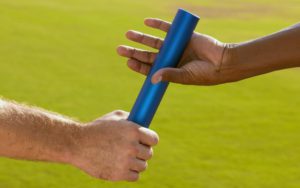
A famous step toward perfection in a lean production system is a lot size of one. However, few people realize what enormous effort and rigor Toyota applies to achieve this goal. During my visit to a Toyota plant and the APMS conference in Tokyo in 2015, I saw quite a few stunning examples of this quest. Let me show you …
Can you tell your Bottleneck from your Inventory?
On the shop floor it is common wisdom to find the bottleneck based on the inventory. If the buffer is full, the bottleneck is downstream. If the buffer is empty, the bottleneck is upstream. Is this true? My student Carolin Romeser and I spent quite some time verifying this, and found some interesting results. In general it is true, but … the devil is in the details.
How to Make “Just in Time” Work – Part 1

Just in Time (JIT) is the delivery of parts just when you need them. In my last post I explained what JIT is all about. In this post (and the next one) I will go into much more detail on different measures you can take toward JIT. But be warned, most of them are not easy, either in implementing or in convincing cost accounting about it beforehand.
What Is “Just in Time”?
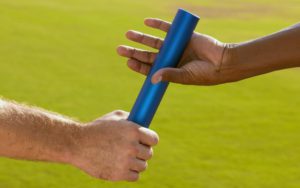
Just in Time (or JIT) is a powerful method to reduce costs and increase efficiency. However, it is also very difficult to achieve. Most times when a Western company tells me it does JIT, it turns out that this is merely wishful thinking. Let me tell you what JIT really is. I will also talk a bit about the history of JIT. Finally, I will show you a few negative examples of wishful thinking common in modern industry. In my next posts I will go into more details on how to make it work.
How Product Variants Influence Your Inventory
The sales & marketing department often aims to create more and more product variants to target even the smallest niche in the market. Yet, it is common wisdom that more variants also mean more inventory.
However, the relation is not quite as clear cut. In my last post I wrote about the Relation between Inventory, Customer Takt, and Replenishment Time. The relation is similar for variants, and it all depends on the ratio of the customer takt to the replenishment time.
The Relation between Inventory, Customer Takt, and Replenishment Time
Inventory is helpful for a fast delivery of goods. If you have it in stock, you can deliver to the customer right away. In that respect, more inventory is better. Yet, at the same time, inventory creates cost, some visible, some more hidden. Hence, one of the goals of lean is to reduce inventory and therefore reduce cost. During my research I stumbled on a very interesting relationship between inventory, customer takt, and replenishment time. Let me elaborate …