If imitation is the sincerest form of flattery, the OEE (Overall Equipment Effectiveness or Efficiency) is indeed one of the most appreciated measures in lean. I counted at least eight different variants and adaptions of the basic OEE – although let me tell you that I am not impressed with all of them. Many of them seem to be theoretical academic constructs with little meaning for your shop floor. Also, identical acronyms and similar terms are often used in a completely different way, adding quite a bit to the confusion. On top of that, I think the OEE is used way too much in industry where it does not make sense, and many OEE numbers are heavily fudged. Anyway, let me show you the many different flavors of the OEE.
KPI
Good and Bad Ways to Calculate the OEE
There are different ways to calculate an OEE. I know of at least three different ways. However, some of them are easier and more practical than others.
Maybe you have seen a formula similar to OEE = A x P x Q. I see this formula often, but for me it is a very impractical way to calculate the OEE. Let me show you why by comparing the three different ways to calculate an OEE.
The Problems of Cost Accounting with Lean
Accounting is one of the cornerstones of the modern economy. Cost accounting in particular helps in decision making with the goal to maximize profit. Many decisions are based on these numbers. Unfortunately, cost accounting usually does a really poor job of capturing the essence of manufacturing in general and lean manufacturing in particular.
Lies, Damned Lies, and KPI – Part 3: Countermeasures
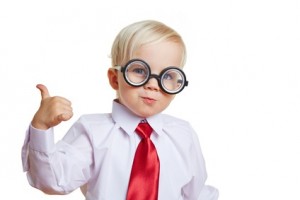
There is an inflation of key performance indicators (KPIs) in industry. In my last posts I have explained how KPIs are often wrong, and why bad and fudged KPIs are a huge waste. Yet, you cannot really run a larger corporation without KPI. In this post I will finally give some advice on (1) what you need to do to measure good KPI, and (2) how to avoid fudged KPI.
Lies, Damned Lies, and KPI – Part 2: Effects of Fudging

Modern manufacturing works with a lot of performance measures, often called key performance indicators (KPIs). Unfortunately, they are rarely accurate, and often even intentionally misleading. In my previous post I described some examples of commonly manipulated KPIs. In this post I would like to explain the ugly consequences of incorrect or manipulated KPIs. In a final post I will also show some ways that you can reduce this negative effect. But first, how do bad KPIs (and hence most KPIs) hurt your company?
Lies, Damned Lies, and KPI – Part 1: Examples of Fudging

Statistical measurements, usually called key performance indicators (KPIs) are found on pretty much every shop floor and in every company. Many management decisions are made based on KPI. Unfortunately, these numbers often are not reliable at all.
Mark Twain popularized the phrase “Lies, damned lies, and statistics.” Winston Churchill famously said, “I only believe in statistics that I doctored myself.” Hence, both men were wary of trusting numbers. You should be too!
A Successful Example of Lean Implementation – Trumpf and its Synchro Manufacturing System (Part 2)
Half a century ago, Toyota started to develop its Toyota Production System, the archetype of every lean manufacturing system. Almost every manufacturing company nowadays seems to try to implement lean manufacturing. At the same time, most also seem to fail miserably, creating a lot of huff and puff with little benefit. However, occasionally there are (very) few companies that have implemented lean manufacturing successfully. Trumpf and its Synchro production system is such a successful example of Lean manufacturing, and one of the finest production system for machine tool builders. Due to the length I have split this post into two parts. This is the second part.
A Successful Example of Lean Implementation – Trumpf and its Synchro Manufacturing System (Part 1)
Almost a century ago, Toyota started to develop its Toyota Production System, the archetype of every lean manufacturing system. Almost every manufacturing company nowadays seems to try to implement lean manufacturing. At the same time, most also seem to fail miserably, creating a lot of huff and puff with little benefit. However, occasionally there are (very) few companies that have implemented lean manufacturing successfully. Trumpf and its Synchro production system is such a successful example of Lean manufacturing, and one of the finest production system for machine tool builders. Due to the length I have split this post into two parts, the second part being available here.