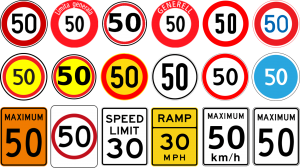
Value stream maps are usually drawn using standardized symbols…or that is what most people believe. While there are some symbols that are used pretty much universally, other elements have different symbols in different organizations or by different sources. Other identical symbols are used in a different way by different organizations. And, every day people seem to invent new symbols. In this post I will (try to) give an overview of what is out there, along with my opinion on what I use frequently and what I usually avoid.