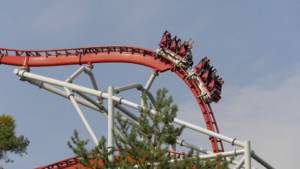
CONWIP (Constant Work in Progress) is an easy way to establish pull production for custom-made products. Traditionally there is only one large loop for the product. However, there may also be situations where it is sensible to split a longer CONWIP loop into smaller segments. Let’s have a look at the details.
Introduction
The most famous pull system is kanban. However, since the part information is constantly attached to the kanban card, it is not suited for small quantities, exotics, custom orders, or in general any product that you do not want to have in stock (Make to Stock, or MTS) but rather produce only when you need one (Make to Order, or MTO).
CONWIP is used to create pull production for Make to Order parts. A card goes around similar to a kanban card, but the product information is removed after completion, and the next product to be produced is taken from a backlog list of open orders. I wrote a whole series on CONWIP starting with Basics of CONWIP Systems. This post looks in detail at the placement of the CONWIP loops. I discussed a bit of it already in my post Frequently Asked Questions on CONWIP Systems – Part 2, but I felt like I need to go into more detail.
One Single All-Encompassing Loop
One option that is always possible with CONWIP is to make one all-encompassing loop. This is easiest for straight flow shops.
If there are branches (e.g., if the product needs sub-components), then the CONWIP card would have to initiate the production or purchase of these sub-components too. The available CONWIP card gets assigned a job from the backlog, which automatically releases additional work orders for the sub-components, but these are all associated with the single CONWIP card for the end product. No new CONWIP cards are introduced for the sub-components. The start of the work on the sub-component may be timed to start at the same time, later, or even earlier than the work on the main component to make sure the component is likely to be ready when it is needed.
If the system is a job shop, the routing of the product is different for different products, and the final route may not even be known in advance, then it is also possible to have a single all-encompassing CONWIP loop. The product just moves through the system with the CONWIP card.
This is actually the approach as intended by the inventors of CONWIP, Hopp and Spearman. However, while it is the easiest to set up, there may be situations where you could benefit from smaller loops. It is also sometimes suggested to use a separate CONWIP loop for every possible routing. However, for job shops this would quickly turn impractical. For flow shops on the other hand it would rarely be needed.
Loops for Different Segments
It is also possible to make loops for different segments or groups of machines. The challenge is now managing the transition from one loop to the next loop. The output of the preceding loop is now the backlog for the next group.
This is extra work. Hence, you should not do this just because it is possible, but only if there is a valid reason for it. This is based on my previous post Frequently Asked Questions on CONWIP Systems – Part 2. A couple of the situations are exceedingly rare for Make to Order CONWIP cards.
- Supermarket in front of the customer: This is a common place for the CONWIP loop to end. The loops the customer uses for your products may not be relevant for you.
- Supermarket for large distance between processes: This may help you to reduce fluctuations by creating separate buffers in separate CONWIP loops.
- Supermarket for change of responsibility: Definitely! The ability of humans to blame others may be easier to handle if they are on separate CONWIP loops. So, unless you enjoy the blame-game, a separate loop may be helpful, although it is not a cure-all solution.
- Supermarket in the case of high demands on flexibility and reaction time: Shorter loops make you more agile and allow for re-prioritization at different backlogs. Be aware that this is more work though!
- (Rare)Supermarket for process-specific lot-size differences: A rare situation for Make to Stock, and exceedingly rare and unlikely for Make to Order. You would need an order that you split into different batches with separate CONWIP cards, and subsequently have a machine with a different batch size. If this applies to your product, consider revising the batching and CONWIP rules rather than splitting a loop into two.
- (Rare) Supermarket when creating different variants: While this is common for Make to Stock, it is exceedingly rare for Make to Order products, since the definition of a Make to Order product is that it is assigned for a specific customer.
Loops for Individual Machines
Finally, you can give every single machine its own CONWIP loop. This is of course the most complex solution. However, it gives you the finest level of individual workload of the machines and allows frequent re-prioritization. This is actually now becoming very similar to the POLCA (Paired-Cell Overlapping Loops of Cards with Authorization). See my series of posts starting with “What Is POLCA?” for more details.
Which One Is Right for You?
That is a tough question. The answer is of course, “It depends.” Try to find a compromise between the additional effort of creating and maintaining separate loops, and the benefit these loops give you. Do not underestimate the effort to maintain loops! It is easy to make a few lines on paper, but it takes constant work and vigilance to keep a loop in good condition. Here especially the re-prioritization can be challenging (although there are many companies that do it successfully using POLCA). For job shops you have the additional problem of managing the routing. You would have to do that anyway, but it adds another layer of complexity to the problem.
On the Hand-Over
Regarding the hand-over of the material, there are two options. You could consider completed parts outside of the previous loop, and the CONWIP card is sent back as soon as the part is completed at the last process within the loop.
My preference and recommendation, however, would be to keep the CONWIP card attached with the parts in the loop until the subsequent process or customer actually takes the part (or in the worst case, the part is scrapped or disassembled if the customer’s order was canceled). Otherwise you risk overproduction, and your system is no longer a pull production, losing all the benefits of pull production.
So, I hope this was interesting to you, even though it went into a more-detailed aspect of pull production. In any case, go out, make sure your material is flowing in pull production, and organize your industry!