POLCA stands for Paired-Cell Overlapping Loops of Cards with Authorization and was developed by Rajan Suri around 1990. It is sometimes mentioned alongside kanban and CONWIP as a production control system. Let me explain to you how POLCA works. In my next post I look at the pros and cons of POLCA. In my last post of this mini-series, I will show you the calculation for the number of POLCA cards, including some critical comments.
The similar-sounding word Polka is also a Czech dance music and textile pattern, hence the colorful illustration of the polka dots on the left (don’t worry, more technical diagrams will follow below).
How It Works
POLCA is designed for job shops, systems of work centers, or systems of cellular manufacturing of high-mix low-volume or customized parts. The jobs may move differently from machine or cell to another machine or cell. Between each possible pair of machines or cells, POLCA establishes a loop similar to a kanban loop. However, instead of kanban or CONWIP, these cards are called POLCA cards. As the name implies, these loops are overlapping. You also need to calculate the order release dates for the different jobs at each cell or machine.
The Overlap
A simple example is shown below. A product came from machine M1 to M2, and will go to M3 next. Coming from M1 to M2 the product had the M1-M2 POLCA card attached to it. Continuing to M3 it will receive the M2-M3 POLCA card from the subsequent loop. The product will be processed at machine 2 only if a) there is a M2-M3 POLCA card available and b) the order release date for this product on M2 has passed. If either the product order is not yet released for M2 or there is no M2-M3 POLCA card, the order will not start at M2.
Once the product at M2 is completed, the M1-M2 POLCA card goes back to M1 to permit the processing of the next product at M1 (a loop can have multiple POLCA cards). Hence there is a pair of loops with POLCA cards that overlap at every machine or cell, hence Paired-Cell Overlapping Loops of Cards.
Elements of POLCA
A system using POLCA needs three elements for control:
- At the beginning of a larger system is a list of open orders that are released for the first production step.
- Between each pair of machines or cells, there is a loop with POLCA cards. Each POLCA card is assigned to one and only one loop, but it is not assigned to a certain product (unlike kanban).
- You need to calculate the order release time for each order in the list of open orders and each machine that it will pass though. For example, order 4711 can be started at the earliest at the first machine on Monday 11:00, the second machine Monday 14:00, and the third machine Tuesday 8:00. This is often done through an overarching ERP system.
There is little information needed on a POLCA card. Most important are the source process and the destination process. For management it is also helpful to know the index number of the card in the loop, and the total number of cards in the loop. A barcode can also help.
Please note that this card does not necessarily have to represent only one item. A POLCA card can also be used for batches of material. If your batches get too large, however, you may consider using multiple POLCA cards for large batches.
For larger systems it may be better to implement these cards virtually in an ERP or similar computer system, where a computer keeps track of the cards as well as the release dates.
Rules of POLCA
The operator has to follow a few simple rules in using POLCA. Suri calls this the “Decision Time.” These rules are also shown in the flowchart.
- At the beginning, the operator should check if there are any available open orders in the list of open jobs for his cell or machine where the order release time has passed. If there are no open orders left that he can do, he should find work at another process or cell. This may involve a supervisor assigning him to a new task.
- The operator takes the next available and released job.
- The operator checks if he has the right POLCA card available from the subsequent process that allows him to start the job. If not, he repeats the process with the next open order (except for the last process in the POLCA system, which has no subsequent process).
- The operator checks if he has all the material needed to start the job. If not, he repeats the process with the next open order
- After these checks the operator processes the job.
- Afterwards the operator returns the POLCA card of previous loop to the previous process to release more jobs.
A Few More Details
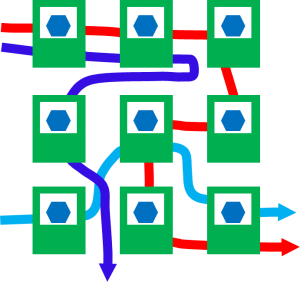
In the original literature on POLCA (sources below), it supposedly works only with manufacturing cells (although it is not defined what exactly the author sees as cells). However, as described in more recent literature, it would work also for any general job shop with multiple machines or processes. It would even work for a larger system where different sub-units are merged together. It is not suitable for flow shops. It is also not really helpful for mass production.
POLCA is sometimes called a push-pull hybrid. While the author uses an, in my opinion, incorrect definition of pull in his book (see my post The (True) Difference Between Push and Pull), the result is correct. The number of POLCA cards limit the inventory to a hard upper limit between two processes. The multitude of possible process loops does water it down a bit, but this is still pull. The order release time calculated by an ERP system, however, is definitely a push aspect of production. If it would only be the order release time, it would be easy to overstuff the system with jobs. However, since both the order release time and the POLCA card are needed for processing, it is in the end still a pull system.
So, after explaining to you the basics of POLCA, in my next post I will do a bit of a review of the advantages and limitations. Overall it is a feasible method. In my last post I will talk about the way to calculate the number of POLCA cards, where I may be a bit more critical. Overall it is up to you to decide if this method will work for you or not. Nevertheless, I hope this is insightful to you. Now, go out, and organize you industry!
Sources
The original book by Suri is Suri, Rajan. Quick Response Manufacturing: A Companywide Approach to Reducing Lead Times. Portland, Or: Taylor & Francis Inc, 1998.
Suri just published another book: Suri, Rajan. The Practitioner’s Guide to POLCA: The Production Control System for High-Mix, Low-Volume and Custom Products. Productivity Press, 2018.
While doing my research I also found the book by Hermann Lödding helpful, although to my knowledge it is available only in German: Lödding, Hermann. Verfahren der Fertigungssteuerung: Grundlagen, Beschreibung, Konfiguration. 3. Aufl. 2016. Berlin Heidelberg: Springer Vieweg, 2016.
P.S.: This series of blog posts is based on a question by Vyacheslav Goncharenko.
P.S.S.: I would like to thank Rajan Suri for his input and his patience.
Hi Chris,
thank you very much for the post.
Slava
I am in the process of implementing POLCA in a low-volume, high mix manufacturing facility. Does anyone have suggestions on where we can purchase work order packets with card slots and/or boards for the POLCA cards? Looking for off the shelf solutions and not reinventing the wheel. Thanks a lot!
Hi Tom, there a re a number of suppliers for material to organize a material and/or information flow. I like Orgatex, they have good quality and service, but are also not the cheapest. You could also ask the inventor Rajan Suri for recommendations (link at the very end of the blog post).
Hi Christopher,
the first time I heard/read of POLCA was in this blog post and since then I found it very interesting and promising. But there is this one question, to which I found no answer yet, nether on the web, nor in the books:
In an job shop environment, wouldn’t it be much less complex to not create individual POLCA-cards for each cell combination but, instead, create one shop floor board, where each cell publishes its POLCA-cards as free capacity signals. The POLCA rules for authorisation stay the same. Each supplier-cell (cell A) could simply check the board if there is a free capacity signal from the subsequent cell (cell F), take it off the board and connect it to its production order. No special A/F-cards needed… What are your thoughts about that???
Thanks a lot!
Marcel
The question is: Do you want the information (the cards) at the machines, or at a central location? I would put it wherever there is less walking for the people who need the information. Managers usually prefer a central location (since it is less walking for them), but this may not always be ideal. Depends on the layout and set-up of your shop floor.