Mitsubishi Motors is the oldest of the major car companies in Japan, established 1917. It is also one of the smaller ones in Japan, with only slightly more than 1 million vehicles produced in 2016. In January 2018, I had the chance to visit their Okazaki plant near Nagoya. I also visited the Mitsubishi Fuso plant in Kawasaki and one of its suppliers, although that is technically another company. Let me give you the gist of the Mitsubishi Motors Plant Okazaki.
Introduction
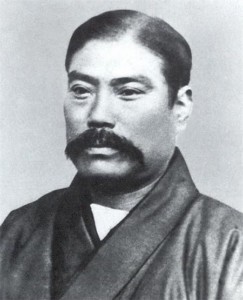
The famous three diamonds of the Mitsubishi group date back to 1870, when Yatarō Iwasaki (1835–1885) started a shipping firm. This eventually became the biggest industry group in Japan.
They built their first car in 1917, although it was no commercial success. They built their first commercial vehicle in 1932. During World War II, they were one of the major weapons producers in Japan.
After the war, the US Government dismantled these industry groups and the company was split in different parts. Eventually in 1970, Mitsubishi motors was created as an independent company. Mitsubishi frequently had partnerships with foreign car makers, and in 1990 was rumored to try to take over Honda. Mitsubishi Fuso for their trucks and buses was established as a separate company in 2003, with Daimler being the largest shareholder, holding currently 89% of the shares.
As for corporate responsibility, Mitsubishi Motors does not have a good reputation. There were multiple scandals, dating back to 1970, where they covered up defects and manipulated their fuel efficiency. Their (former) president, Kawasoe, along with other managers was arrested and convicted. Mitsubishi Motors suffered, and retreated. Their Australian plant was closed in 2005, their European plants shut down in 2012, and by 2015 they closed their US plants. Eventually in 2016, Nissan achieved a controlling stake of 34%. Hence, nowadays Mitsubishi Motors is controlled by Nissan (the Nissan-Renault-Mitsubishi alliance), and Mitsubishi Fuso by Daimler.
The famous three diamonds were merely a rock in the jewelry box of someone else, and the morale of many employees suffered from this humiliation. According to Vorkers.com, Mitsubishi workers are among the unhappiest in the Japanese automotive industry with an average ranking of only 2.6 out of 5 (Toyota 4.2).
Statistics
Mitsubishi Motors still has five plants in Japan, plus a few in other parts of Asia. The Okazaki plant had a total of 5,500 employees, of which 3,000 were working in manufacturing, with the others in development and testing. They work in two shifts from 7:30 AM to 4:30 PM and from 7:30 PM to 4:30 AM. Toyota once had a similar shift pattern, but changed it after their employee relationship crisis in 1990. They have up to two hours overtime on top of these hours if they do not achieve their daily goal.
Their line takt was sixty-three seconds per vehicle (or fifty-seven cars per hour), producing around 1,000 cars per day, or around 500 per shift. The monthly goal was 20,179 vehicles for January, up from 18,428 in the previous (holiday) month. The assembly line produces in lot size one, and every car on the line can be of a different model.
Information Flow

Mitsubishi Motors seems to use kanban to control their material flow. A lot of the picking of kits is also done using pick-by light. They work in teams with an average size of fifteen people (1,100 blue-helmet workers managed by seventy white-helmet supervisors).
I saw andons showing the target quantity for the given time (286 cars at 14:17), the actual quantity produced (265 cars) and the gap (-21 cars) as well as the total target for the entire shift (501 cars). They had two types of andon lines, a yellow warning line and a red stop line that stopped the line in case of problem.
Material Flow
Interestingly, for the assembly of the axles and the engine, they turned the car sideways. Later for other assembly work, the car was oriented forward again as shown below. Besides the orientation, this is actually part of a new concept at Mitsubishi (and similar at Toyota) where they try to have an assembly line that can easily be moved or rearranged. The key point is that all equipment is floor mounted or even just put on the floor rather than hanging from overhead. At Mitsubishi, this is called a Tatami Conveyor (畳コンベア ), and Okazaki is their first plant with this system. I have written more on this concept (with focus on Toyota) in a previous blog post on the Continued Evolution of the Toyota Assembly Line.
Like many other automotive plants, quite a bit of the material is provided in the form of kits that travel along the body on an AGV. As it is common in Japan, these AGVs use inexpensive plastic pipes to create a shelf superstructure.
Very interestingly, they use golf carts as AGVs. I have seen stripped-down golf cars as AGVs before with storage for parts on top, but Mitsubishi uses the entire golf cart for pulling between one and three carts behind it! These are standard golf carts, upgraded with a computer for self-driving and some red/yellow/green status lights on top. They use around two hundred of them for longer distance transport. These golf carts transfer the goods to smaller shelves or AGVs next to the assembly line.
Overall, the material flow felt organized, although it seemed to be more material than what I was used to at Toyota.
Efficiency
There seems to be still some hand-welding, painting, and coating. But tires, seats, gas tanks, and dashboards are installed with the help of a mechanical arm, although they do not have a raku-raku seat that goes along with it (mechanical arm with a seat so the worker can comfortably slide in and out of the car while sitting).
Still, there was lots of manual work, especially overhead work. It may have been just my impression, but I thought I saw a lot of people rubbing their back or rolling their shoulders in discomfort.
As for their production efficiency, I observed around 40% value-added time during the axle assembly and 50% during the final assembly, putting it on the average of Japanese automotive assembly, but far behind Toyota with 70% to 90% value-adding time for their workers. This did not include the problem that caused the stop of the entire line for thirty minutes, which supposedly has never happened before. I hope someone someday will fix this “NeverHappenedBefore” thing, because it seems to be happening everywhere all the time all over the world 🙂 . (The only other possibility would be that these “NeverHappenedBefore” things happen only if I am in the plant, in which case I would obviously be the cause … somehow.) In any case, the line utilization was supposedly 95.7%.
If You Want to Follow in My Footsteps …
The tour at Mitsubishi Okazaki was a larger tour with fourteen people. It is one of the very few automotive tours in the world where you can also see (part of) the paint shop and the stamping shop. For registration and the visit, you would need to speak at least some basic Japanese and have to call the plant. They were also the only plant that required me to put stickers on my mobile phone cameras.
Summary
The plant was clean (although the paint shop was smelly, which is somewhat unavoidable) They also had a nice training area next to the line with a focus on safety, similar to Toyota and Scania. Overall, the plant gave me the impression of a good average Japanese automotive plant. Particularly noteworthy was that they included the paint shop in the tour, and that they use almost unmodified golf carts for material transport. I enjoyed the visit. Now, go out, and organize your industry!
Series Overview
- The Grand Tour of Japanese Automotive – Overview and Toyota
- The Grand Tour of Japanese Automotive – Nissan
- The Grand Tour of Japanese Automotive – Honda Sayama
- The Grand Tour of Japanese Automotive – Honda Kumamoto
- The Grand Tour of Japanese Automotive – Mitsubishi
- The Grand Tour of Japanese Automotive – Mazda
- The Grand Tour of Japanese Automotive – Suzuki
- The Grand Tour of Japanese Automotive – Subaru
We are Travelling to Japan & Staying in Nagoya Area on 6th May 2019.
we are a group of 25 Engineers who would like to visit the plant,
Hello Vinay, check the following link (in japanese, maybe use google translate) https://www.mitsubishi-motors.com/jp/csr/contribution/local/factory.html . You would need a translator or a japanese speaker to accompany you.