Honda is the largest motorcycle manufacturer in the world with around 17 million motorcycles sold in 2017 (compared to number 2 Yamaha with around 5.2 million, 2015 figures). In January 2018 I had a chance to visit their Honda Kumamoto plant. This plant gave me a much better and very different impression than the Honda Sayama automotive plant.
Introduction
The Honda Kumamoto plant was established in 1976 and is the largest Honda plant in Japan by area. It is their main plant for the production of motorcycles in Japan including their engines, but it also produces garden power tools, generators, and four-wheeled scooters.
A major earthquake in Kumamoto in April 2016 damaged the plant, and it reopened and scaled up production again during the summer of 2016.
Statistics

The plant includes casting, welding, stamping, machining, and painting operations, but my visit focused on the engine and final assembly lines. There are around 3,300 employees in the plant, 8% of them being women.
Honda Kumamoto has multiple assembly lines for engines and motorbikes. The main lines are dubbed the “Fun Line” for the big motorcycles and the “Multi Line” for the small vehicles and scooters. It also has a line for the generators and other products.
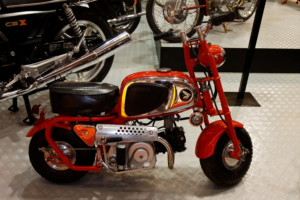
All lines produce in lot sizes of around thirty to fifty vehicles. The takt time is around 2:30 minutes for vehicles, and around five minutes for the other products (generators, power garden tools, etc.). Each motorbike line has a capacity of around four hundred bikes per day. The motorcycle lines had powered carts on tracks going around.
The Fun Line was around 150 meters long with thirty workstations. This line also had fancy monitors at each station tracking process time and often also had details like counting the number of screws tightened to prevent a missed screw. The other lines did not have these digital displays. The Fun Line was actually split into two loops with different types of carts. The first segment had around sixteen workstations and the second segment around twenty to twenty-five stations. They used an overhead crane to move the parts from one segment to the next. The Multi line had only one segment. They use a running changeover, where they simply keep two carts empty for the five-minute changeover process.
Overall Impression
The plant was squeakily clean. Quite a contrast to Honda Sayama. In Kumamoto, the white uniforms were actually white! It was much more organized and seemed to have much less material. The different shifts and functions were indicated by pins and labels on the sleeves and caps. For example, the first shift had an orange “1,” and the second shift a blue “2” label on the hat or sleeve. Also, while the workers in Honda Sayama were in a good mood, the workers at Honda Kumamoto were outright cheerful!
Information Flow

While Sayama did not use kanban, all material in Kumamoto was kanbanized and they used pull systems. Very good! However, like Sayama they also have no andons or andon stop lines or buttons. The only visual indicators were red/green stack lights on some selected machines. Hence it was difficult to understand how much was produced, or if they were on track.
Unlike Toyota, Honda does not stop the line in case of problems. All quality issues continued to be assembled and moved through the lines to be sorted out at the end. These issues were fixed in a separate repair area. This repair area was about half as large as the entire line. When I visited, there were about sixty motorcycles in the repair area, or around two hours’ worth of production, on top of another forty or so motorcycles that were also parked around there, blocking walkways. Altogether, the repair area was the most chaotic section of an otherwise reasonably well-organized plant. Toyota does this much better.
Material Flow
The material flow was overall good. All of the carts with frames were height adjustable and adjusted their height to match the ergonomic height of the particular assembly. For the smaller Multi Line, they could also be rotated. One particularly short employee also had a raised platform about 10 cm high, 4 meters long, and 1.5 meters wide to work more comfortably.
Honda uses kitting extensively, where workers prepare a kit of parts for the motorcycle. Some material is also supplied by shelves along the line. They said that they do not have issues with mixing up the kits (i.e., not a kit too much or too little during the batch changeover).
For the first segment of the Fun Line assembly, the cart pulled a shelf with the kit behind it. The kit was assembled directly on the line before the frame of the motorbike was put on the cart.
The interesting part, however, was the line layout. This line had lots of zigzags as shown below in a top-down view. The advantage of this is that due to the curve the rolling shelf and the cart with the motorcycle are closer together. Thus it is less walking distance for the operator to go and get a cart. This also meant that operators were working on both sides of the line. Please note that if my Japanese serves me right, they told me that they patented that idea.
The second part of the Fun Line also used kits, but these were prepared on the floor above. These kits were provided hanging from an overhead railing on both sides moving along with the cart. There was always one shelf hanging, and a separate hanger for the larger front module. These hanging kits were also height adjustable separate from the motorbike carts. Hence, the parts in the kit were always at an ergonomic height for the operator. This is illustrated below. Please note that these hanging kits were actually on both sides along the motorbike (about 1.3 meters away so the worker could move between kit and bike), rather than between the bikes as shown below.
Besides these hanging and pulling kits and the carts themselves, all of the material transport that I have seen was by hand, pushing movable shelves around the factory. There was not too much material around, and the ratio of material and assembly area was good (except of course for the rework area, and one spot where seventy Goldwing fronts – three hours of production – were waiting).
In some spots they also used karakuri kaizen tricks. I also noticed that all the power tools hanging from overhead were hanging quite low, almost at knee height of the operators. Here they sacrificed ergonomics for quality, to prevent these hanging tools from banging into, scratching, and denting the product.
Shift Change
I was also able to observe the shift change. The plant runs in two shifts from 7:00 AM to 3:45 PM, and from 3:35 PM to 12:00 AM, and yes, there is a ten-minute overlap.
- Most workers from the second shift arrived shortly before 3:30.
- At 3:30, music starts to play for the typical exercise that is very common in Japan. It is called “Rajio Taiso” (ラジオ体操) for radio calisthenics, which was introduced in 1928. Every kid in Japan learns these. Most but not all of the employees of the second shift participated, although some did it very sloppily, moving only the hands rather than the entire arm. The exercise ends at 3:35.

- From now on, it is paid time. Between 3:35 and 3:40, the team leader has a meeting with his team. A team leader at Honda Kumamoto is in charge of around ten operators (Toyota: only four), and the team leader I observed had a team of twelve people.
- At 3:40, the second shift walks to the line.
- Between 3:41 and 3:43, the line stops completely for the handover. The workers of the first and second shift exchange information.
- At 3:43, the line starts again. From now on the second shift is working.
- At 3:45, the work time of the first shift is over, and people were leaving (although some put in a few more minutes to count and arrange materials).
Efficiency
As usual, I estimated the percent of value-adding work by counting what workers were doing when I looked at them. At Honda Kumamoto, it was similar to Honda Sayama with workers actually creating value slightly below 50% of the time (Toyota 70% to 90% value add). However, as the cycle time is longer, I would give some credit to Kumamoto, and say that considering the differences in products, Kumamoto is a notch above Sayama in terms of efficiency.
If You Want to Follow in My Footsteps …
… then you would need to speak Japanese or at least have an interpreter. They do tours also for individuals (in my case, I was the only one on my tour). You also need to apply through their website, but it is much less hassle than for Sayama. I got a very personal tour and was able to influence what I could see. Many thanks to Honda for the tour! Their address is 1500 Ozu-machi, Kikuchi-gun, Kumamoto Pref. , Japan.
Summary
So, overall I did like the plant. It is not on par with Toyota, but it is clean, and they put a lot of work in efficiency and material supply. They also use pull to obtain material. Now if they could only get the remaining information flow right and install andons and stop the line when there is a problem.
Also many thanks to Honda for allowing me to visit and observe their plant. In both cases, I got a very personalized tour, and the tour guides were able to accommodate the special requests of curious me to see this and see that.
I learned a lot and got quite a few ideas especially from Kumamoto. I hope writing about this also gives inspiration for your work. Now, go out, get your material flow in order, and organize your industry!
Series Overview
- The Grand Tour of Japanese Automotive – Overview and Toyota
- The Grand Tour of Japanese Automotive – Nissan
- The Grand Tour of Japanese Automotive – Honda Sayama
- The Grand Tour of Japanese Automotive – Honda Kumamoto
- The Grand Tour of Japanese Automotive – Mitsubishi
- The Grand Tour of Japanese Automotive – Mazda
- The Grand Tour of Japanese Automotive – Suzuki
- The Grand Tour of Japanese Automotive – Subaru
Hi there!
I really wanted to get my dad into a tour but I was told they need a group of a minimum of 10 people with a translator.
Could you share how and/or what application you used to do the tour alone?
Any information would be soooo appreciated!
HI Cynthia, i do speak Japanese, hence I was able to book a tour for 1 person. Language is often a problem in Japan. Only Toyota and Mazda offer english tours.
Hi,
Could you please share an email to contact the factory.
We would like to visit the factory.
Hi Pirjo, the website is in Japanese, and could be translated using google translate. However, you would need to speak Japanese or have a translator in order to visit.
I live in US and love Honda bikes, I do have 4 of them and plan to ship all in Europe, the problem is that EU custom ask for emission numbers, actually which
EURO category EURO I,II,III,or IV these bikes fell (cause they will charge me
for that) can you help me I can e mail to you VINs and models (GOLD WING,
FURRY,SHADOW,VFR 1200)
I have had over 40 motorcycles in my life and still got 10, the goldwing is a fantastic bike for long trip, i just wanted to know where it was manufactured. long range fuel-comfortable-handling is above average. funny enough i had a honda 4 (750) in 1975 and never had another honda until 2021..