In my last post I described the pacing of pulse and unstructured flow lines. Another common way to structure the pacing of flow lines is the continuously moving line. In this type of line, the parts are always moving, and the processes and workers move along with the part until the process is completed.
Continuously Moving Line

In the continuously moving line, the parts are – as the name says – continuously moving. This is usually an automatic transport system like a conveyor belt, a moving walkable platform, pulling by an underground chain, or moving hanging carriers, to name just a few.
These systems also have their advantages and disadvantages. They are, for example, very common for the final assembly of cars. Let’s look into more detail in the set-up and operation of such a continuously moving line.
Speed of the Line
One very important aspect of the continuously moving line is the speed of the line. The speed is usually set through a central system. Adjusting the speed of the line requires some thoughts.
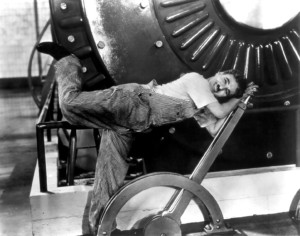
Henry Ford and his managers, around 1920, simply kept on increasing the speed of the line until the workers were no longer physically able to keep up with the speed. Luckily, these times are long gone (I hope). But seriously, don’t just increase the speed until the workers can no longer take it! This is really bad practice and will demotivate workers. They will hate the company, and quality will suffer. In lean terms it would be one of the three evils in manufacturing: Muri, or overburden. See Charlie Chaplin in the afternoon scene of his famous movie Modern Times on how NOT to do it (Youtube link here, but copyright unclear).
Definition of Speed
At this time I have to be more precise in what I mean by speed. The speed is usually defined in meter (or feet) per second (or minute). However, when setting up a line, the speed is actually the time between one part and the next part. The distance between parts is important here. Every how many seconds does a part enter the space of a station. This is the time the station has to complete the part.
See, for example, the animation below. The parts in the top line move faster than the parts in the bottom line. On the other hand, the parts in the bottom line are much closer to each other than in the top line. Overall, the speed of the workers is the same in both lines, as is the number of parts produced. In the bottom line, however, the stations are much closer together, meaning that the workers have less space, but also that the overall floor space is better utilized.
Hence, the actual line speed in meters per second also depends on the spacing of the parts. Therefore, it is often better to talk about the time between parts rather than the speed of the line. Of course, once the line is set up, the speed and the time between parts are directly related.
The time between parts should be based on two things: 1) The station or process with the highest workload (and of course, with line balancing, all stations should have a similar workload), and 2) the customer demand.
Not Faster than Slowest Station

The time between parts should not be faster than what the station with the highest workload can do. The slowest station should be able to complete the part within that time.
There is a little wiggle room if you alternate high-workload parts and low-workload parts. For exaple, for a car assembly, if you alternate two-door and four-door cars, then the door assembly has to do, on average, three doors. If the line is set up so that this team has a long-enough segment of the line to average this out, it may be a possibility to briefly have a higher workload if it is followed immediately by a lower workload. To determine the workload, you can use either time measurements of predetermined motion time systems like MTM.
Adjusted for Customer Demand

The second influence for the time between parts is the customer demand. If your demand is lower than expected, you can reduce the speed of the line and give your workers more time. There are actually two schools of thought here. One is to reduce the speed and give the workers more time, the other is to reduce working hours and keep up the speed.
Toyota, for example, does reduce the speed of its assembly lines slightly if demand is lower. However, this is only a small reduction of 10% to 30%. For larger decreases in demand, they reduce the working time rather than the working speed. The danger of reducing the speed too much is that the workers have too much time, which will break their working rhythm and may worsen quality. They also have to find their rhythm again if the line speeds up again.
Also, from the view of the worker, working too slow is a pain and does feel uncomfortable and boring. If you don’t believe it, try it out. The next e-mail you type, force yourself to slow down to one letter per second. Instead of enjoying the additional free time, it will feel r-a-t-h-e-r u-n-c-o-m-f-o-r-t-a-b-l-e. The same applies to manual work.
By the way, it should be obvious, but if the customer demand is higher than your line at top speed, then you need either more work hours or a second line or a significant improvement of efficiency of the stations.
Other Influences on Speed
There are additional influences, as for example that the speed is significantly slower than walking speed (i.e., significantly less than 1.4 meters per second). First of all, the workers have to keep up with the parts. Unless there is an entire moving platform, the workers may have to walk along with the part. The part should be slow enough so that the worker can not only walk along, but also work while walking along. This also would usually satisfy another requirement that a worker does not get injured if a part bumps into him.
Length, Spacing of Parts
Each station should have enough space so that it can do the work before another part arrives. Since we can play around with work space, speed of the line, and time between parts, we can influence the work space through the other parameters. In the interest of efficient usage of space, we should have the smallest work space possible that provides a safe and comfortable working environment. Also, the smaller the work space, the less walking and transport distances you have.
Advantages

The moving assembly line has quite a few advantages.
First, the production output can be defined through the line speed. This makes it difficult for workers to slack off. While this is usually seen as an advantage, it can also be seen as a disadvantage, as the worker needs some short times to recuperate. However, due to the fixed speed, the work stations are often slightly faster than the speed, giving the worker some breathing room again.
It is also easy to see delays and problems. If there is a problem, the workers have to stop the line before their time runs out. Check my post on Andons for more about a good way to signal such problems and to stop the line.
The moving line also needs no part buffers. Since the speed is exactly the same everywhere, there are no extra buffers of parts needed to decouple fluctuations. Instead, your fluctuations are decoupled through waiting time of the workers for the next part.
Disadvantages
The moving line also has disadvantages. To operate, the line has to be fully staffed. Adjusting the capacity through the number of workers is usually more difficult.
The workers also have more wasted as part of their work. They have to walk along the part during production (unless it is a moving walkable platform where the workers can walk on the moving platform while it is moving), and they definitely have to walk back to the next part after finishing one part. Since the speed is also slower than the slowest station, their work may include waiting times for the next part.
The moving assembly line is also difficult to automate. For workers it is not a problem to walk back and forth along the line. However, this is more difficult for machines. While small handheld tools are often hanging from a movable overhead system, it is difficult to have a complex machine moving along the line. But then, the main advantage of defining the line speed is not needed for automated systems anyway, since you can set the machine speed directly, whereas the worker has to be influenced by the speed of the line.
The moving assembly line is also less suited for long cycle times, and is most commonly used for shorter cycle times. I have seen it most often in automotive, where a car is produced every 1 to 2 minutes.
Overall, if you have manual mass-produced parts with a short cycle time, a moving assembly line may be a possible solution. Now go out, get things moving, and organize your industry!
Just out of curiosity, in Germany and other places in EU, are factory workers paid by the hour or salary? Say, if the demand drops to the point where there isn’t enough work for the day and workers get sent home early, do the workers get paid for the full day, or just the hours worked?
Hi Andre. It is usually a salary, but they track the hours (e.g. 35 hours per week are common, plus 25 or 30 holidays, plus public holidays, plus – and this may be a surprise to you if you are from the US – sick days). There is often a performance related component where they can get extra money for up to (usually) 30% more production than regular.
Ugh… you guys have it good there. Here, it’s strictly $/hour, and 50+ hour 6-day weeks are common. Given the crummy pay, working more hours is the only way to make ends meet.
If there is no work to be done and people get sent home early, that means less pay for the workers. Yesterday, I was working on a line at a pump assembly plant, and the line lead was seriously stretching the time to make it a full day while the production quota was only about five hours’ worth of work, if that. The management are too busy in the office fudging numbers anyway.
I totally get what you mean about overly slow work being uncomfortable. Towards the afternoon, it got to the point where I just told a coworker that I’m just going go help on another line at that one station where one person consistently does the work of two people with WIP piling up in front of them while everyone is having an easy day.
*whispers* … universal, affordable health care …
Hi this is what I am searching for very long time. Thanks for sharing. I have one doubt about the ” Space between the products”.
Pls confirm my below words are correct: “The space between the products are must be equal to space between the workstation”
Because then only the operator can perfectly meet the product based on conveyor velocity.
Note: Here we can adjust conveyor velocity is equal to takt time.
Thanks in advance.
Hello Lingesh,
This definitely would work, but you also can give them less space if they have less workload. Assume a line with a part every minute, and the workers taking 1 minute per part (and lets ignore fluctuations for now). A worker that would need only 30 seconds would need only half the space, and have 30 seconds waiting time for the part. The next worker could then be “30 seconds” closer to the start of the line, and start 30 seconds earlier. This next worker still needs a minute, but this is fine.
Obviously this does not work for a worker that needs 2 minutes, since the next part arrives before he is done.
Very good question!
Hello Christoph,
You stated, quote: “The danger of reducing the speed too much is that the workers have too much time, which will break their working rhythm and may worsen quality”.
The way how I saw it done at Toyota was that a reduced TAKT led to a rebalanced line to always fully load the member. I have not seen a line takt change where the work content stayed the same!
Hi Holger. What I learned at Toyota was that they adjust the speed of the final assembly slightly depending on demand. It seems that they did not re-balance the line – which may be tricky for an entire automotive assembly line. But again, these were only smaller changes.
Hello Christoph.
Your posts about pacing of flow lines are very clear. It’s hard to find such plain definitions. You helped me a lot.
I have one doubt about the difference between pulse line and continuous moving line. It seems that they both have three advantages: requires no buffer, easier to identify potentials, and easier to define the speed. Their disadvantages are also similar, and continuous moving line has an additional disadvantage of less suitable for long cycle times. Does continuous moving line have any advantage over pulse line? (The answer must be yes, since continuous moving line is generally used in auto industry, but I don’t know what is the advantage.)
Hi Albert, that is a very good question.
* One advantage of the continuous line is that you don’t need to start/stop the line every takt.
*It also can allow workers to work on the incoming next part already, which gives a bit more flexibility for mixed model lines.
On the downside, tools and machines may have to move along with the line.
I hope this helps. It certainly made me think 🙂
Addendum: Just added this to the blog post. Thanks for the suggestion! “Another advantage of the continuous line is that you don’t need to start/stop the line every takt. The continuously moving assembly line also has no sharp start/stop for a takt, and hence workers can start a part a bit early or finish a bit late, as long as they catch up with the next part. This gives more flexibility for mixed model lines.”