A kanban is, in its basics, information to reproduce or reorder parts. Hence, in its most basic form it has to say “make me this part” or “bring me this part.” While such very simple kanban systems are possible, usually it helps to include other information on the kanban card. In this post I want to talk about the design details of a kanban card, especially what kind of information we should include on the card. Please note that the items on the list below are suggestions. Which ones you actually include depend on the system you want to establish.
Physical (or Digital) Form of the Kanban
A kanban can have many different forms, including paper cards, paper in a protective folder, digital, a box or container, a piece of metal, or pretty much anything that goes with it. I usually prefer containers or metal pieces since they are less likely to get lost and are often easier to implement and visualize than an digital ERP system kanban. For details on different physical kanban types, see The Problem of Losing Kanban – Different Kanban Types.

Also, for simple system you may consider a triangle kanban, i.e. a special type of Kanban system with only one kanban. The triangle kanban is used if a lower limit on inventory is reached. In this case, the triangle kanban indicates reproduction of a fixed quantity of parts. The remaining inventory after the triangle kanban is large enough to cover the replenishment time. Named after its originally triangular shape at Toyota (since it was cut from scrap metal, which did not yield good rectangular shapes).

Part-Related Information

Now we have to think about what kind of information we include with our kanban. A kanban card stands for one or more parts. Hence, first and foremost, you need information related to the part. In all of the examples below, I assume you have a physical sheet (a card or a label on a box). For digital kanbans, the required data is similar, but now you have to link it in your ERP system.
Part Number: Probably the most relevant information is the part number. In a proper modern manufacturing system, every part type has its unique part number, usually an alphanumeric string. It could look like, for example, T2232-55675-A2322. The computer can identify the part using this number. On a side note, Toyota also sometimes uses additional shorter 3 digit codes that are valid only within a certain part of the value stream. These three digits are easier to remember, and help users to identify the part within their own working area (Thanks to Damien for the info).
Part Name: Humans usually don’t know all the part numbers (although many of the people working with these numbers often know quite a lot of them). In any case, it helps to write out in plain English what the part is.
Quantity: Finally, you should write down the quantity of parts this kanban card stands for. A kanban card can represent exactly one part. However, if you have a lot of parts of this type in the system, it may make sense to use one card for a box or container with multiple parts. A kanban card may stand, for example, for a box of twenty parts. If you represent multiple parts with one kanban card, I strongly recommend getting a container or box that fits this number of parts. This way it is easier to keep track of the parts if you take them out of the container one by one. If you have smaller packaging units in a larger pack (e.g. boxes on a pallet), you can also include this information, e.g. 20 packs of 5 pieces each (Suggestion from Rob – Thanks Rob!).
Unit: This is related to the quantity. If your kanban card for screws says a quantity of twenty, is this twenty screws, or twenty packs with fifty screws each, or twenty kilograms of screws? Often, this may be obvious, but it is usually good practice to include the unit.
Picture: This is not very common, but you could include a picture of the part on the kanban card. This may be helpful for humans to know what they’re looking for.
Important: While you can also put a lot of technical details about the product on the card, think carefully if a kanban is really the right place to add the information (Suggestion from Rob – Thanks Rob!).
Material Flow-Related Information
Type of Kanban: There are different types of kanban. Most often you distinguish between a production kanban and a transport kanban (withdrawal kanban). A production kanban issues the reproduction of a new part. A transport kanban merely orders another part from a preceding supermarket or general inventory. It helps to write on the kanban if it is a production kanban or a transport kanban so you don’t mix them up and accidentally produce a part instead of delivering it. You may even think about using different colors to distinguish the two types. Also, depending on the type, the following information may differ.

Packaging: A kanban card can also include packaging information. Is it a pallet, a pallet cage box, a cardboard box, a standard size industry plastic box, etc.? This helps to know how to ship the goods.
Source: Where does the material come from. For a transport kanban, this may be the warehouse or inventory where the material is taken out. For a production kanban, this may be the production line that reproduces this part. This information can also be set up in different levels. You could indicate the source as it is known to the workers (e.g., “housing line” or “inbound warehouse“). You could also use the ERP numbering system for the inventories or systems (e.g., “L23-5” or “I225/4“). For loops between plants you could add not only the line or inventory, but also, if necessary, the plant or warehouse (e.g., “Detroit East” or “Kentucky II“), which again could also be added using the ERP code for these locations.
Destination: Similarly, where does the material go. Since it is a kanban, the destination should be a supermarket. Again, you should write on the card where the material goes, often both in human-readable form and in ERP code, possibly also including the plant location.
Information Flow-Related Information
After the part and material flow-related information, we now look at the information flow.
Index Number: First of all, it is really helpful to number your kanban. If you have twenty kanban for one part type, you should number them from one to twenty. This really helps if you want to check for lost kanbans (e.g., if all kanban cards but #13 are repeatedly passing through the supermarket as part of their loop, then it is possible that kanban card #13 got lost and needs to be replaced).
Total Number of Kanban: How many kanban are in the loop for this part number. This may be helpful information for anyone checking or trying to understand the system. On the other hand, in a kanban system it is often good practice to experiment by adding and removing kanban to improve the number of kanban. In this case, you would have to either exchange all kanban in the loop or have a wrong total number of kanban (or you could just skip this information altogether).
Kanban Loop: You may have a name and/or number for the kanban loop to uniquely identify the kanban loop where the card belongs. This is not always used but may be helpful depending on your situation.

Lead Time: Some cards include additional data like lead time or replenishment time. Personally, I find this less helpful, as the lead time can change quite a bit over time, and I wouldn’t need this on a kanban card. Still, some people like it that way. You decide if it is helpful for you or not.
Contact Person/Department: The kanban card may also include a contact name of the person or department that issued the cards and is responsible for the upkeep of the kanbans (not necessarily the machines).
Order Date and Due Date: This is possible for kanban cards that are printed from an ERP system, where the paper printout is thrown away and reprinted whenever the “kanban” leaves the supermarket. In this case you can include the additional information for the order date (time) and the due date (time) for this cycle of the kanban card through the kanban loop. However, this information is cumbersome if you reuse the kanban cards. (On the other hand, this information is helpful if it is a closely related CONWIP card for made-to-order goods).
Digital Readability
The kanban card can be read by humans, but nowadays it is often useful to have it in a machine-readable form.
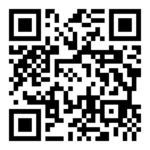
1D/2D Bar-code: A bar-code in either the classical bar code form or a 2D code that can store more information. In this case a simple handheld laser scanner will make it much easier to transfer information from the card into your ERP system.
RFID: Another option is to include a RFID chip (radio frequency identification). Rather than with a laser scanner, this works through radio communication. While this also works if the code is dirty or not in the line of sight, this approach has other issues (e.g., with shielding by metal parts).
Other Information
Company Logo: Often, kanban cards include a logo or name of the company. Strictly speaking this is not necessary, but it is something companies like to do.
Good Practice for Kanban Card Design
There are a few things to keep in mind when adding data to the kanban card.
Priorities: Which information do you really need? You have limited space, so use it for the information that is necessary and don’t overload the kanban card. Some information on the card is more important than others. For example, the part name, part number, and bar code are probably the most important information. Mixing these up will lead to lots of problems downstream. On the other hand, the index number of the kanban, for example, is infrequently needed.
Readability: Print the important information using a larger font. Keep in mind that not all of your employees may have 20/20 vision. At least the critical information should be easy to read.
Labels: This should be obvious, but do label the fields or boxes. If you have a box with the number “20,” it helps to know if this is the quantity, the packaging type, or the ERP code for the source.
Colors: You may be able to do the kanban cards in different colors. This may help your people. You could, for example, distinguish production and transport kanbans by color. You could also distinguish high runners from exotic parts, indicate source or destination, or use color to create priorities (see this series of posts for more on priorities).
Clarity: Do avoid choices or options for the operators. For example, if a transport kanban could get parts either from “Warehouse A” or “Warehouse B,” it will lead to confusion and waste. The same goes for “If … then …” kind of information. Instructions like “If Warehouse A has more parts than Warehouse B, use Warehouse A” is a sign of a ill-designed kanban system that leads to waste. Luckily, those kinds of thing seem to be very rare (or I just did not yet go to these places).
Very Simple Kanban
Depending on the complexity of the products in the kanban loop, you may not need all this information. Toyota sometimes uses simply color coded washers or balls to inform the preceding process on what to produce. As shown in the image, a red washer with a round hole would mean a red part, a blue washer with a square hole would mean a blue part. If the information is clear for the supplying process, then these systems also work.
Simplest Kanban
The absolutely simplest kanban is of course no kanban at all. If the supplying process and the supermarket are right next to each other and the product variety is small, the worker can simply be instructed to always fill up the supermarket, starting with the part that has the most gaps (in the image this would be the red part). It is still a pull system, even though it has no kanban anymore.
Overall, the actual design of the kanban is not quite as easy, and a few things can be considered. Please do take the time to think about this when designing kanban cards. Now, go out, print some kanban cards, create a pull system, and organize your industry!
Hi Chris,
Good post, I agree on all elements. Just a few small remarks:
– knowing that a kanban in a loop always relates to something typically called a handling unit, the kanban typically includes the content of the handling unit as “packs X units”. For instance, a kanban related to a pallet of 20 containers with 6 pieces, would read 20 X 6 (assuming of course this convention is well-known in the plant).
– withdrawal and production kanban can also be distinguished using card size.
– use the color of the card to indicate the source (for production cards) and source and destination (for withdrawal cards). The color is an easy way to visualize the “address” from/to where cards and parts should come/go in my experience.
– don’t put to much product specifications on the card (sometimes I see this tendency). If they change, you need to replace al cards or the cards become inconsistent with the product definition. A kanban should not replace the product data sheet.
– when you need to group cards (for batching purposes) at a product family level (e.g., to create campaigns), it is sometimes wise to color-code or identify the campaign on the card. Be careful here, as a card can move to several operations requiring possibly different campaign groupings.
– in MTO environments, I tend to use the order sheet/file typically attached to the product from the start.
Best regards, Rob
Hi Rob, Very cool suggestions. I added some of these info’s to the article. Thanks for helping me to improve my posts 🙂
Great read……….
This article was a great read and provided very useful information that will help me with my green belt project. My team is analyzing our company’s kanban cards and discovered that some are inaccurate, which is leading to inventory inaccuracies in the system. I had just become familiar with the kanban cad at the beginning of this project and this article helped explain what is typically on a kanban card and what else could be helpful to add. I believe that it is very important for the kanban card to include the source of where the material came from. This allows for workers to be able to easily find the material in the warehouse. I also believe that the prioritization of information on the kanban card is very important. Kanban cards with complex information can be easily misread. Lastly, I found the suggestion of color differentiation of kanban cards to be very useful. For my project all Kanban cards are currently the same color, perhaps color differentiation could increase efficiency.