In flow shops, you have a production line of some sort. This may be an assembly line or a manufacturing line; this may be automatic or manual. In lean, you often hear about the famous U-line.
While this is a great solution, it may not fit all problems. Depending on the surrounding conditions, a different line layout may be beneficial. This post is the first in a series on line layout. In this post I would like to discuss what you should consider when designing a new line layout. The next post will look at actual line layout options.
The Big Picture
The first thing you would have to consider is the big picture. What is the overall material flow in your plant? In other words, where is your inbound warehouse or receiving area, and where is your outbound warehouse or receiving area? Take for example the image shown. The inbound warehouse is on the left, and the outbound is on the right. A good line design would follow the overall material flow and go from the left to the right. A bad line design would go in the opposite direction, requiring you to transport all material through the plant twice. And, as you surely know, transportation is one of the seven types of waste (muda) that should be reduced or eliminated.
This is similar for systems where the inbound and outbound warehouse is combined. In this case, a “loop” starting and ending near the warehouse would be best. A loop in the opposite direction would be worst, since again you would have to transport the material through the entire plant twice.
Similar applies if your line supplies or receives material not from the warehouse but from another production location. It would be good if the line starts closer to the source and ends closer to the drain of the material flow.
While this sounds obvious, you would be surprised how many plants forget this simple big picture when designing a line or even a complete plant. Naturally, for existing plants it may not always be possible to get a perfect material flow due to the historic development of the plant over time. But at least try not to make it worse.
The Surrounding Conditions
Before you go into more detail of the line layout, there are a few things that you need to consider beforehand for a good line design.
How Much Material Has to Go to (or from) the Line?

Obviously, some material has to go in on one side and come out on the other side. However, how much material has to be provided at the different steps in the line? For an assembly line, this may be a lot. For a manufacturing line where, for example, a part is milled, drilled, stamped, and cut, this may be next to nothing. Depending on the amount and especially the size of the material, you may have to consider how to supply the material. Does it come from the sides or only one side? Can it be delivered overhead or from the floor above, or is there even an underground conveyor or delivery system? Can it be handled by hand, or do you need a crane or other mechanical lifting device? Do you need forklift access to the processes? Do you need milk run stops and space for small supermarkets?
Is It an Automated Line, or Are There Operators Working?

Naturally, if there are operators you would need space for them. Additionally, operators may be able to work on multiple machines. You may have heard of the famous U-line (more below), where the U-shaped line allows an operator inside the U to handle multiple machines with less walking distance. At the same time you don’t want to deliver material where operators are working, but rather from the other side if possible. If you don’t have operators, then this is not a constraint. If you don’t even have materials, you have to consider only maintenance access.
Is There Shared Equipment?
If your line (or lines) have to share one or more processes, it may be a bit more complicated. The lines have to merge at the shared process and then split up again.
Naturally, there are many more factors that influence the line design, like number of variants, customer takt, etc. Additionally, physical constraints like support columns or exit doors also influence your final design. For this post, however, we only look at the layout and leave the details to other posts.
What Are the Conditions of Your Shop Floor?

If you have a greenfield location where you build a new plant, you are in luck. You can design the line any way you want and then just build the building around it.
In most cases, however, you do not have this luxury, but have to fit your line in the building you already have. In this case many other considerations come into play. Where do you have space? Are there certain processes or locations that cannot be moved? Such Process Monuments may be a large stamping press where you have not only the press but also infrastructure underneath the shop floor. Moving such a press may be prohibitively expensive.
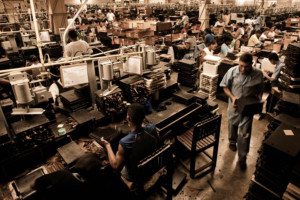
What is your overhead space? Will your machines actually fit in? What is the carrying capacity of the floor space? Some heavier equipment may exceed the carrying capacity of some more delicate shop floors. One example I have heard was a company delivering a heavy machine using an even heavier mobile crane when they learned that there was a parking garage underneath. The driver went white as chalk and immediately drove back out very, very slowly. Luckily the floor did not collapse.
Where are your support pillars for the roof? These are the bane of any line layout designer, especially if they are not shown correctly in the technical drawings of the plant! A smaller issue is often access to pneumatic lines or certain gas lines.
Conclusion
Overall, there are a lot of things to consider when designing a new production line. The points above are just to get you started. In my next post I will look at actual line layouts. This includes I-shaped lines, S-shaped lines, L-shaped lines, and or course the famous U-shaped line – although while the U shape is good, it is not a perfect solution for everything. So stay tuned. In the meantime, go out and organize your industry!
Having worked in various industries from making women’s Bras to making MACK TRUCKS, one very important fact to consider is your product Type (size, wt., can it be hand moved or need crane/ conveyor/etc.??
Absolutely true. I added a sentence to that respect into the blog post above.
Waiting for the next part. Looks very interesting
Very interesting, simple to read and gets the message across.
Thank You
Thanks. Simple and clear information to understand.
Really useful in practical sense and easy to understand.