
There is often a distinct lack of appreciation and good manners toward shop floor employees. Yet, lean manufacturing happens on the shop floor. Not in Excel, not in PowerPoint, not in meeting rooms. As such, you need to become part of the shop floor in order to change the shop floor. For this, you need the support and goodwill of the people on the shop floor. The first step to getting their support is to have good shop floor manners. Due to the length of the post, I have divided it into two posts. These two posts will give you some guidelines on how to behave on the shop floor. (The second post is here)Nevertheless, the executive summary for both posts can be found at the end of each post.
A Short Problem Description

It is surprising how often managers, consultants, and other outsiders strut through the shop floor like they own the place, clearly signaling that they are better than the workers. Even if they indeed own the place, some small appreciation of shop floor etiquette will do wonders in forging a successful manufacturing system.
Also, all to often people are just ignorant about others. I once coached two trainees on a lean project. Two nice guys, friendly and very comfortable to hang out with. As part of this project, they went to observe a process with me watching them observe. After three minutes of intensive observation and note taking, I stopped them and asked if they had missed something in the preparation for the observation.
After some reflection, they brought up all kinds of ideas like getting more data, looking at the layout, making a better value stream analysis, etc. Neither of them thought about the worker at the process. None of them even noticed her beyond that she was part of the process. As I said before, these guys were nice and friendly. Yet they treated the worker like a mere piece of equipment.
Of course, this was not intentional. After I pointed this out, they apologized profusely to the worker and me, then introduced themselves and their work. But until I pointed it out, they didn’t even notice the human being as a human being. Please don’t do that!
Different Roles
Naturally, different visitors to the shop floor have different roles, and small differences in shop floor etiquette apply. For example, if you are an external visitor, it may be sensible to announce your visit a few days beforehand. On the other hand, such an announcement would make no sense at all if you are the plant manager.
Similarly, if you focus on one or a few particular processes, it may be sensible to spend more time introducing yourself to the people working at these processes. On the other hand, if you walk through the entire plant, this may be neither feasible nor sensible.
If your reason for the visit is only to understand the current situation, shop floor operators may be satisfied with a quick note. On the other hand, if you plan to change the situation on the shop floor, you would be well advised to spend more time informing the workers of your reason for the intended changes, and especially the impact on the workers.
Rules are also different depending on whether you are part of a large group that may hinder workers or you are a single person who is much less in the way of everybody else.
Also, keep in mind the local languages. In northern Europe, Belgium, and the Netherlands, even normal shop floor workers speak a bedazzling amount of foreign languages, so you may be fine with English. For example, while working on a dutch shop floor, I asked the blue collar worker if he preferred English or German. “Either one is fine,” was his answer in flawless English.
Nevertheless, you may need an interpreter for some plants abroad (e.g., in China). I know of one group that worked with an interpreter in China, but nothing worked with the employees until after a week when they figured out that the interpreter spoke Mandarin and the locals spoke Kantonese, two totally different spoken languages. In my view, however, the embarrassing thing was that it took them a week to figure it out!
Overall, depending on the details of your visit, you may have to adjust the guidelines below.
Shop Floor Etiquette Rules
Below are a couple of things to keep in mind if you want to have a good interaction with the shop floor. Of course, you also can’t make everybody happy all the time. Change is not always welcome. But having a good standing on the shop floor will make it more likely that the change is accepted. Hence:
Announce Your Visit
Ideally, a few days before your visit, inform the shop floor management about your visit (who, where, why, when). The team leaders of the areas you visit should then briefly inform the operators. This way any questions can be sorted out before you arrive. Note: Make sure you inform the correct shift. It doesn’t help if the morning shift knows about an visitor in the afternoon (Don’t laugh, this has happened way too often 🙁 ). Naturally, this is only sensible for visitors who do not commonly visit the shop floor, as, for example, top-level executives from other locations, external consultants, or other external visitors.
Introduce Yourself in Person

Whenever you are observing a process on the shop floor, you should introduce yourself to the people working there. Say hello, state your name and affiliation. Then explain what you do and why (see next point). Be open, be friendly, and follow the rules of etiquette. For example, in Germany it is customary to shake hands. In Asia a polite bow is appropriate (with the angle depending on the rank of the people involved). And in the US, a friendly “How are you?” or similar is common. Using first names or family names also vary with regional customs. In the US it is often fine to use first names, while Europe reserves first names for close friends and Asia uses first names for dogs and children only). Skipping such details will reduce the positive effect of your introduction.
Of course, if you are not observing a specific process but rather walking through the entire line or plant, it may not be feasible or even sensible to introduce yourself to everybody. In this case, a general announcement may suffice.
Explain What You Do and Why You Do It
Now that you are here, the workers want to know why. If you plan to change things around, then you should spend quite a bit of time describing what you are doing and why. For the workers, the most interesting part is what will change for them. This is also the part where it may get tricky.

Based on prior experience, workers probably believe that all negative aspects of the change will be much worse, whereas all positive aspects may or may not come. Hence, depending on your changes, this discussion may be a minefield. For example, if your goal is to reduce headcount by 10%, you better have an absolutely waterproof reason (e.g., the workers are needed on other lines/for new products). Otherwise it may be better to skip this step of “what” and “why” altogether.
Naturally, if you only visit to see the plant, you may also skip this step. In most plants I know, workers are accustomed to a “five-minute flyby” by top executives, where the plant manager does his best to hide the true situation anyway (See How to Misguide Your Visitor – or What Not to Pay Attention to During a Plant Visit!).
Do Not Make the Work More Difficult through Your Presence
This should be obvious. The workers on the shop floor usually have quotas and numbers to meet. Often, their pay depends on performance. If you mess things up for them, you may hurt the plant and – even worse – their income. In any case, they will like you less. Here are a couple of examples on how you can make or avoid trouble for the workers and hence in the long run for you.

Do not block the workers’ access to wherever they need to go! If you and your group cluster around a process, workers and material supplies may not get through. Make sure to get out of the way. Make sure that the workers know that they can tell you to move if you are in their way. If necessary, break your group into smaller subgroups so that twelve people are not standing around one process, but maybe four people around three different processes. Similar applies to driveways. Try not to block forklifts or milk runs. Also, if you are in a larger group, inform all group members to pay attention to the workers’ needs.
Also, keep an eye out for safety light barriers! These things will bring a machine to an emergency stop whenever someone or something goes through the barrier. It is important for safety, but it is also an annoyance for the workers if visitors walk through and their work stops. And, for the visitor, it is quite embarrassing to have brought everything to a standstill. Believe me, I know!

Keep your noise down! A shop floor is usually already loud enough, but a larger group walking through can make things worse. In a larger group, it may also be difficult for everybody to hear the speaker. However, this is NOT a good case for a megaphone. Instead, use smaller radio-controlled headphones and a microphone.
Also, do not touch anything unless you really, really know what you are doing! For example, when I was young and inexperienced, I had the opportunity to see a plant making some small metal parts. At one point in the process, I picked up one part from a conveyor, looked at it, and put it back. With a sigh, the operator took this part and the three before and after it and chucked them in a bin. It turned out that the parts were washed, and now had to be washed again thanks to me. Learn from my mistakes.
Still, I was much better off than another person having a guided tour through a foundry. He saw a piece of metal on the floor and picked it up to look at it. He quickly found out that it still was 1000°F (ca. 500°C) hot, resulting in third degree burns on his fingertips.
If you schedule a meeting with workers, be on time! Depending on the situation, you may even arrive early. For example, if you want to observe a changeover, don’t ask the workers to wait until you are there. Instead, be there early and wait until the workers are ready to do the changeover.
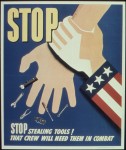
And, of course, the most obvious rule: Do not take souvenirs without asking for permission! Any part on the shop floor is (usually) there for a reason, and a missing part may bring the entire plant to a complete standstill. Hence, do not take anything with you without permission (also known as stealing).
The second half of this “miss manners” for the shop floor is in the next post. However, if you can’t wait, just read the summary below.
Executive Summary
Below is a summary of the guidelines of the two posts (Part 2 is here). Not all of them apply to every person or visit, hence use your common sense.
- Announce your visit
- Introduce yourself in person
- Explain what you do and why you do it
- Do not make the work more difficult through your presence
- Do not block the workers’ access to wherever they need to go
- Keep an eye out for safety light barriers
- Keep your noise down
- Do not touch anything unless you really, really know what you are doing
- Be on time
- Do not take souvenirs without asking permission
- Appreciate their work
- Take your hands out of your pockets
- Do not bring anything to eat or drink
- Do not overdress for the occasion
- Listen to their input
- Get permission beforehand for taking times/photos/videos
- Follow regulations
- Do wear the required safety equipment
- Wear clean room garments or similar
- Follow other rules and guidelines
- Say thank you and good-bye
- Follow up
- Inform the people you have worked with about the results
- Show the appreciation through a small gift
Love this!!