In my last post, I started to show the main reasons why EPEI leveling with a fixed repeating schedule so often fails (for details on EPEI leveling, see Theory of Every Part Every Interval (EPEI) Leveling). This post continues with more reasons and also gives some advice on how to reduce the damage or even increase its chances of success. It also has a suggestion for a test to determine if your system is ready for leveling.
Again, there seems to be a lean religion that claims that putting up a leveling box will lead to salvation. Well, Lean is not a religion or magic. Lean is hard work, and you actually need to understand what you are doing. Just copying something without understanding is a good way to fail, especially with leveling.
More Reasons Why EPEI Leveling Mostly Does Not Work
Limited Power Over Supplier and Supplier Ability
A leveling system (like most other lean manufacturing systems) depends on the ability of the suppliers to deliver in full on time. However, it takes time to develop your suppliers. Toyota has been working on this for decades, including by sending people over to help suppliers to improve.
The Western approach is often very different. Rather than helping the suppliers, Western customers often use threats to force the supplier. This is usually not a viable strategy, even if you have power over the supplier (as, for example, a car maker usually has over its suppliers).
Additionally, not every customer has power over its suppliers. If your orders are only a small share of your supplier’s business, then you can expect other bigger customers to receive better treatment. Any supplier would rather ditch your 5% of his sales than endanger the 40% of his biggest customer, even if he would not tell you this. Quite frankly, you would probably do the same. In sum, getting your suppliers to deliver in full on time is hard work on both sides, and does not simply happen just because your management has decided that leveling is the latest fad.
Does Management Want to Be Cheated?
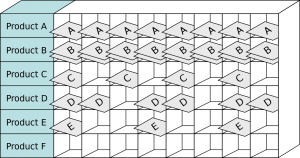
Sometimes it feels to me like management wants to be cheated. Of course they would prefer to have a working leveling system. However, if they can’t have a working system, they may also settle for something that looks like one, even if it doesn’t work. Most often, however, they simply don’t know if the leveling system is counterproductive.

One of the easiest ways to look like you have a working EPEI leveling system is to install a Heijunka Box, where the cards represent the production schedule. No matter if it works or not, these boxes usually duly impress management and give the appearance of a lean shop floor. Often, this box is all you need.
Just to make sure, I definitely prefer not to do EPEI leveling with a shop floor that cannot do EPEI leveling. I also don’t want to do dog-and-pony-shows with my management. However, if you are ordered to establish EPEI leveling, you are obliged to try or risk the consequences. In this case I would try my best, even knowing fully that it does not work. However, I would try to limit the damage.
How to Limit the Damage of EPEI Leveling
Some EPEI leveling creates havoc with the exact manufacturing system that it is supposed to smooth. However, there are some approaches to reduce the damages and to avoid the worst negative effects. Without going in too much detail, these are:
- Create a system to handle change. Try to establish a standard procedure of what to do if there are changes to the pattern to ensure a reliable material supply.
- If external factors like customer demand, material supply, worker availability, or machine downtime force you to change the pattern, do it immediately. Do not try to force the pattern through the system; it will just make it worse. Pretty much the only EPEI leveling systems I have seen that did not end in chaos were those that ditched the pattern at the first sign of trouble. It does not help the smoothing idea, but it prevents it from becoming worse.
- Do not cut off your production plan at the end of the day. You probably will not hit the target quantity every day. If you have capacity left over at the end of the day, continue with the next day’s plan. If you cannot make all parts you were planning to produce in one day, do roll over the remainder into the next day. If you just cut them off you are likely to get delivery problems. If you absolutely feel the need to start a new cycle every day, make sure you have produced your exotics in the morning, and have some additional buffer stock for the high runners that may or may not get produced at the end of the day.
- Try to increase your ability to buffer customer demand swings. These can be done through an increase in buffer stock, but also through increased flexibility in your production capacity. If these options are not possible, the buffering will default to the third option: the customer has to wait.
- Try to minimize the additional organizational overhead. Often, a Heijunka Box is added to make the leveling look good. These boxes can be useful. However, if you also keep the previous ERP-based scheduling system, your people now have to maintain TWO systems. Additionally, they have to sort out what to do if the two systems disagree. Rather than making things easier, it will be harder for the shop floor.
- Keep the leveled interval as short as possible. If you do a four-week leveling interval, you have to fix your production schedule in for more than four weeks in advance, with all the associated problems. Doing a two-week interval halves this (presumably) frozen period. Similar, one week is even better. Of course, the shorter the interval, the smaller the smoothing effect, but since you will have difficulties in following the pattern anyway, there is not really much smoothing to begin with.
Test Your EPEI Ability
EPEI leveling is pretty advanced and has high requirements on the production system. As I said above, only the very best systems have the ability to do EPEI leveling. If you are wondering if your system is an excellent production system ready for leveling, here is a professional opinion: probably not. Sorry! If, despite all my warnings above, you nevertheless want to try EPEI leveling, I would suggest doing some tests first.
In the first test, fix the production schedule for the next few weeks (for whatever leveling period you desire). Afterward, compare the schedule with the actual production on a daily basis, both for quantity and for sequence. This will tell you a lot about your ability to follow a schedule. If this analysis makes you shiver, then don’t do EPEI leveling. By the way, this is also a good test to check if your existing EPEI leveling system is any good.
A second test would require you to get the best possible customer forecast for the desired leveling period. Afterward, check the forecast with the actual sales. Again, if it makes you shiver, then don’t do EPEI leveling. Or at the very least increase your buffer stock to cover these prediction uncertainties.
A Personal Statement
This double-post is a good bit longer than my usual posts. However, I have been planning to write it for a long time and finally got it off my chest. I spent a lot of time seeing failed EPEI leveling systems in other plants, which was just sad. I also spent a lot of time arguing with management about the uselessness of leveling, showing tons of data and analyses, only for the management to decide to go ahead anyway. This was very frustrating. (Although, in all fairness, if even higher-up management wants leveling no-matter-what, then it would be not wise for my own management to oppose. )
Fortunately, as a professor, I no longer have to do the frustrating part, but it still saddens me to see all this misguided EPEI waste in the name of lean. Hence, do yourself (and me) a favor and be very, very wary of EPEI leveling with a fixed repeating pattern. Now go out and organize your industry (but please use one of the other types of leveling that are more likely to work).
Overview of Posts in This Series about Leveling
- Why to do Leveling (Heijunka)
- An Introduction to Capacity Leveling
- Theory of Every Part Every Interval (EPEI) Leveling, Also Known as Heijunka
- The Folly of EPEI Leveling in Practice – Part 1
- The Folly of EPEI Leveling in Practice – Part 2
- Introduction to One-Piece Flow Leveling – Part 1 Theory
- Introduction to One-Piece Flow Leveling – Part 2 Implementation
Also, Michel Baudin wrote a post on Theories of Lean and Leveling/Heijunka on his blog with a review of my series on Leveling. Check it out for further details on Leveling.
Hi
This is the topic that i never understood.
Lean experts say “produce only demands (Ohno’s famous sentence), when order comes it will trigger your production”
But when i see heijunka topic i see that production planning is being made based on forecast not on actual demand.
Forecast means high stock or stockout in the end due to high demand fluctuation
i think i misuderstand some things. Can you please explain this part
And secondly can you explain how toyota is making forecast
thanks