Almost a century ago, Toyota started to develop its Toyota Production System, the archetype of every lean manufacturing system. Almost every manufacturing company nowadays seems to try to implement lean manufacturing. At the same time, most also seem to fail miserably, creating a lot of huff and puff with little benefit. However, occasionally there are (very) few companies that have implemented lean manufacturing successfully. Trumpf and its Synchro production system is such a successful example of Lean manufacturing, and one of the finest production system for machine tool builders. Due to the length I have split this post into two parts, the second part being available here.
Usually I am very skeptical when companies claim how excellent and lean they are (because usually they are not!). However, many credible sources praised Trumpf for its outstanding production system called Synchro. Hence I was more than excited when I got the opportunity to go and see for myself to find out if it really is that good. Now I can fully confirm that Trumpf indeed is an outstanding example of lean manufacturing. Furthermore, it did not simply copy whatever Toyota does (a common mistake), but adapted its system to the needs of a high variety low volume machine tool builder.
The Company
Trumpf, founded 1923, is the world market leader for sheet metal processing machines. With more than 10.000 employees in all continents, the family owned company is also one of the largest machine tool builders in the world.
Its main products are machine tools for flexible sheet metal processing, especially laser cutting and welding but also combined punch and laser processing, punching and bending. It also sells lasers for other uses besides sheet metal cutting, e.g. lasers for the automotive industry with its many laser-based applications or for micro-processing applications such as display and PCB production.
Starting the Change Process
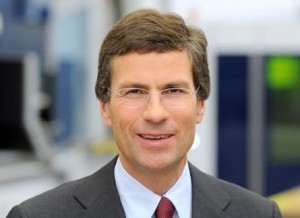
About 25 years ago, Trumpf was like most other German machine tool builders. Outstanding German engineering and top-notch products, but unsystematic manufacturing, postponed deadlines, and excessive inventory. This started to change in 1995, and especially since 2000, when Trumpf family member Dr.-Ing. Mathias Kammüller became head of the machine tool division and responsible for production and quality management.
Mr. Kammüller spent significant time in Japan with a Bosch joint venture, and was able to see the Toyota production system up close. With an enormous motivation and drive he started to implement Lean at Trumpf, changing the corporate culture away from disorganization and towards order. You could say he is the Taiichi Ohno of Trumpf.
The Changes (Part 1)

In 2000, Mr. Kammüller started to roll out his Synchro lean production system. Synchro stands for the Synchronization of man, machine, market, and material. Changes were numerous, including many of the basics of the Toyota production system as for example 5S, Andons, or SMED. However, a few things stand out, into which I would like to go in greater detail
Flow Production

One of the impressive achievements in my view was the implementation of flow production/an assembly line. Implementing an assembly line is easier if you produce lots of similar parts, as for example cars. Machine tools, however, are usually few products with high variety, and hence machine tools are usually assembled on the spot.
Trumpf, however, implemented a flow line. All its (bulky) machines are on hover cushions or on rails, and hence they can be moved from one spot to the next. With about 500 to 1000 units per line and year, they have a cycle time of about 8 hours. Their fastest lines have a cycle time of 1.5 hours. In comparison, automotive cycle times are around 1-2 minutes.
In production theory it is said that a cycle time of 1-2 minutes is ideal. Too little and it becomes boring, too much and the workers need more time to learn the process. 8 hours is about 250 times of the normally recommended time, hence this was one of the challenges for Trumpf. Their cycle times do include a bit of slack for unforeseen events, but not much. The machines also do not move automatically (as with an automotive assembly line), but only at the press of a button.

Interesting is also the adaption to changing demand. In automotive, the speed of the line is increased or decreased. Such a re-balancing of the line would be too much effort for an 8 hour cycle time. Hence Trumpf opts to have an empty hover cushion every now and then if demand is low rather than changing its cycle time.
In automotive with a cycle time of 1-2 minutes, this would be wasted time of the workers. However, if you have a cycle time of 8 hours skipping one cycle gives you a block of time that is quite useable. And Trumpf has a system in place both to predict beforehand when an empty board will come around and to move workers between lines and stations in order to use this time.
Overall, Trumpf managed to successfully implement flow production and an assembly line for its machine tools. These assembly lines are not only a pampered pilot line in a flagship plant, but are installed in all plants for all products worldwide. Furthermore, such flow production also extends to its sub components, with the exception of e. g. the largest lasers of which they sell 10-20 per year. But even there they try to use a sort of cycle time for the different steps, even though the laser itself does not move! Naturally, all production is based on Pull production using a kanban system. At the same time, production of a machine starts only if there is an order. Hence there are no finished machines on stock, which makes sense for such usually customized and expensive products.
Inventory Reduction and Supplier Integration

Yet another success of the system is the reduction of inventory. if you walk through their assembly halls, there is very little inventory compared to what I am used to see at other manufacturers. Their goods receiving area is not much larger than a fancy living room. Depending on the line they have only hours worth of material on site.
They achieved this through different measures. One of the key steps was one piece flow, i. e. the batch size is one. This sounds unimpressive for the machine tools, where every tool is different anyway. However, they also extended this to its sub-assemblies and component manufacturing. For example in milling they can and do produce parts automatically in any sequence. Thus they approach the ultimate goal of Taiichi Ohno and Just-in-Time (JIT): To produce only what is needed, when it is needed and in the amount needed.
Trumpf also extended JIT to their suppliers. Most of the other (failed) JIT approaches simply demand from the supplier to deliver whatever they need whenever they need it, or else they get whacked. With nothing else changing the supplier has only the options to build up stock themselves or to get whacked. In any case it is unlikely to be cheaper.
Trumpf aims to give a reliable and accurate forecast of the demand. The next month demand is fixed, the two months thereafter are not. This system works, and Trumpf has a good reputation with its suppliers, with deliveries actually arriving within their fixed windows. Suppliers also know that if they miss the window, production at Trumpf will stop shortly thereafter due to lack of parts.
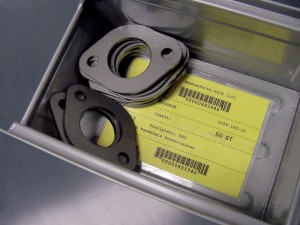
Such a three month forecast of course clashes with changing demand through a Kanban based pull system. Yet suppliers need a longer forecast (or they have to build up inventory and subsequently raise prices). In many other companies the integration of Kanban and Forecast is ill defined. If the forecast tells to produce but the Kanban says no, the decision is often unclear, and usually manufacturing opts to produce to be on the safe side, with resulting excessive inventory. At Trumpf the relation is clear: Produce only if there is a Kanban! If the forecast is too high store the inventory, do not merely shove the problem to your suppliers.
Overall, Trumpf seems to have a very low inventory reach compared with other machine tool builders, or even with automotive companies. While Toyota gets away with a two hour reach (after working on it for 50 years), most other companies I have seen have a two week reach or more. Trumpf with about 1-2 days of inventory reach appears to be quite good.
In the next post I will talk about how Synchro uses KPI’s and team boards, and also how they establish a continuous improvement process. Finally I would like to discuss why Synchro worked where so many other attempts at Lean have failed. In any case, go out and Organize your Industry!
Hi there,
I am a graduate student compiling a presentation about Lean approaches and what companies have implemented them successfully. Could you please list your sources, or at least the “credible sources” that praised Trumpf for Synchro. I would really appreciate it!
Thanks,
Elizabeth
Hello Elizabeth,
these credible sources are people I know within the lean community in Germany. In personal discussions on which companies truly have a good lean implementation, the name Trumpf came up frequently. Additionally, I personally visited Trumpf, and was very impressed with their system (hence the article). If you are looking for academic sources to cite, sorry, I don’t know any. Besides, just because a paper claims a company is excellent does not mean it is so.
Hope this helps,
Chris
HI Chris,
I really want to know the difficulties TRUMPF faced during the implementation of this LEAN concept.
Hi Kal, unfortunately I don’t know the details on that one. I guess there was at least some resistance, since people usually don’t like change.