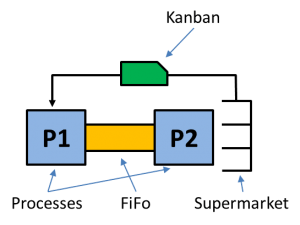
Lean manufacturing pull systems use both FIFO lanes and supermarkets to manage the material and information flow. In my previous post we covered the basics about supermarket and FIFO lanes. Now we go into details about the ten rules when to use a supermarket instead of a FIFO.
To decide when to use a FIFO and when to use a supermarket, here are some guidelines in order of priority. In sum, use a FIFO unless there is a good reason to go for a supermarket. However, there are sometimes good – and sometimes very good – reasons to use a supermarket instead of a FIFO. The ten reasons to use a supermarket are:
- Supermarket for process specific lot size differences (the only hard rule)
- Supermarket in front of the customer
- Supermarket if material flow splits up into different directions
- Supermarket between very different cycle times
- Supermarket between different shift patterns
- Supermarket when creating different variants
- Supermarket for merging of material flows
- Supermarket for large distance between processes
- Supermarket in the case of high demands on flexibility and reaction time
- Supermarket for change of responsibility
As a general rule, you should use a FIFO lane whenever there is no reason for a supermarket. A FIFO lane is much easier to control and manage. Establishing a supermarket usually requires more work to both implement and keep it running smoothly. Hence, unless there is a good reason for a supermarket, you should use a FIFO lane. Therefore, make your Kanban loops as big as possible unless there is a reason for a supermarket. As for the details on the ten reasons for supermarkets, read on…
The Ten Rules for Supermarkets
1: Use Supermarkets for Lot Size Differences
To the best of my knowledge, there is only one situation where a decoupling of the material flow through a supermarket is absolutely necessary – and this is a self-made constraint that can easily be avoided: process specific lot size differences (i.e., when the lot size changes from one process to the next). To be more precise, this is necessary if the lot size of the first process is not a multiple of the lot size of the next process. Below are a few examples to illustrate the point:

If the lot sizes are equal as in example 1 above, then there is no problem whatsoever. If the next process has a lot size that is an even fraction of the previous process (example 2), then there is also no problem. In effect, the second process is forced to have the same lot size as the first process.
Lot size differences, however, are a problem if the second process doesn’t have an even fraction lot size, as in example 3. If you need to use exactly this lot size of 30 every time (e.g. a batch process that fits exactly 30 parts), then there will be either ten parts left uncompleted of the lot size of process 1, or the lot size of process 2 will be short by twenty parts. If the lot size of 30 is only a minimum requirement it will be less of a problem, since you can always increase it to the required number of parts.
Finally, if the second process has a larger lot size than the first process, as in example 4, then there is a risk of not completing a full lot with the second process.
Overall, it is advisable to keep the same lot size throughout the entire Kanban loop. In any case, this hard rule can easily be avoided by adjusting lot sizes throughout the process, and I find this to be a rare constraint in my practical work.
2: Supermarket in Front of the Customer
In almost all cases, it is strongly recommended to have a supermarket in front of the customer. In other words, the last process in your organization should be followed by a supermarket. Hence, the customer can order whatever he wants and you have a reasonable chance of having the product available. The exception is custom-made products for individual customers.
3: Supermarket if Material Flow Splits Up into Different Directions
Another strong reason to decouple the material flow using a supermarket is a material flow that splits up. If some parts go in one direction and others in another direction, then a supermarket will make things much easier.
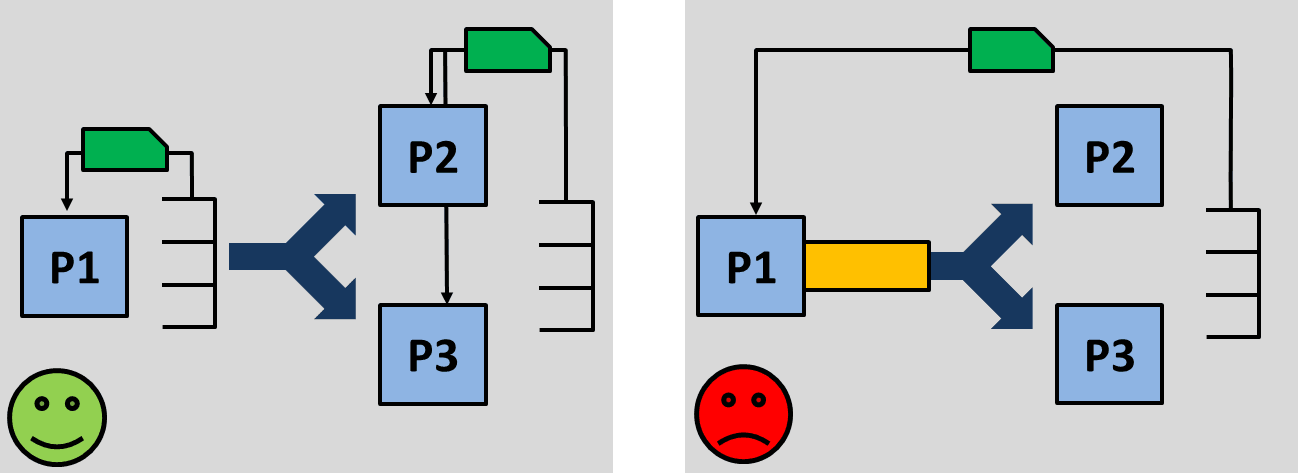
This can be managed without a supermarket, but if you use a true FIFO there is a significant risk that one of your two subsequent processes will be starved of material. For example, if at the end of the FIFO lane is material for process P2, then process P3 would have to wait until the next material for P3 comes down the FIFO lane. If idling processes are okay with you, then it is a possibility, but I do strongly recommend against it.
4: Supermarket Between Very Different Cycle Times
A supermarket is also strongly recommended if two processes have very different cycle times. Coupling processes with different cycle times using a FIFO lane will lead to a lot of waiting time for the faster process. On the other hand, if the process would be decoupled using supermarkets, then the faster process may work on other products in the meantime. If the preceding process is faster, it would be similar to a split of the material flow (see above). If the succeeding process is faster, it would be similar to a merge of the material flow (see below).
Hence, if it’s okay for the faster process to include idle times, then it’s okay to use a FIFO for processes with different cycle times.
5: Supermarket Between Different Shift Patterns
Similar to different cycle times, it is recommended to decouple the material flow using supermarkets for processes with different shift patterns. For example, if one process works one shift per day and the other process works two shifts per day, then a supermarket may help. In this case, the first process has to stockpile enough material to get the second process through the second shift. This material is required regardless whether you use supermarkets or FIFO lanes.
The advantage of supermarkets, however, is flexibility. If problems pop up during the second shift, a supermarket may provide an alternative material, whereas a FIFO lane is stuck with the material in the lane – unless, of course, you manually override the FIFO principle and pull parts out of the middle of the FIFO lane.
Overall, a supermarket will give you more flexibility here when compared to a FIFO lane.
6: Supermarket When Creating Different Variants
A supermarket may also be advisable if the subsequent process creates different variants of the product. For example, if the first process makes housings and the second process adds different elements to the housings. For the same housing, different elements can be added. Hence the second process makes more variants based on the material received from the first process.

In a FIFO lane, the process knows what to produce through the parts coming down the FIFO lane. However, when differentiating into variants, the information has to be conveyed separately (for example, through an attached paper). Secondly, this decision has to be already made in the first process. Hence, all parts coming down the FIFO lane are already earmarked for a certain variant even though the part physically does not require it yet.
It can be done, but a supermarket may be an easier option here. A supermarket avoids the complexity of conveying additional information along the FIFO lane. Additionally, you have the flexibility to use a part in the supermarket for any variant you choose.
7: Supermarket for Merging of Material Flows
A supermarket may also be helpful if material flows merge. The critical aspect here is the timing of the merge of the two material streams. If you can get the timing right, two FIFO lanes can merge. In this case, it’s important that there are always the right matching parts at the end of the FIFO.

For example, Toyota uses two merging FIFO lanes when installing seats in cars. Whenever a car comes down the assembly line, the matching seat has to be at the end of the merging FIFO lane for seats. It is doable, but tricky. With Toyota, there are just too many seat variants to justify a supermarket.
However, if you can avoid this while using a supermarket, you can significantly reduce your organizational effort and your risk of things going wrong.
8: Supermarket for Large Distance Between Processes
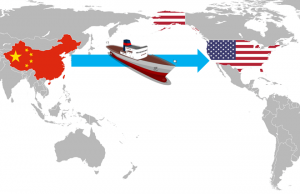
FIFO lanes work very well with processes in close proximity to each other. The farther apart the processes are, the easier it may be to use a supermarket instead of a FIFO. Over longer distance it requires more effort to keep things in FIFO and to know what is coming down the lane. Hence, for longer distances it may be better to use supermarkets.
Granted, you can also make a FIFO over longer distances, but in my experience it often complicates things. This is true the larger the distance is. Having parts shipped from one end of the plant to the other may still be doable by FIFO, but if you import parts from China to the USA, I strongly recommend not using FIFO through ships and airplanes.
Besides the effort necessary to keep FIFO alive over longer distances, the time needed for transport is also an important factor. A supermarket keeps you more flexible than a FIFO, and you can easily change from one product to the next in the following processes. For larger distances you may even consider two supermarkets, one at the sending end and one at the receiving end.
9: Supermarket in Case of High Demands on Flexibility and Reaction Time
The wider the span of a Kanban loop, the easier the system is to manage. However, a wide span also increases the lead time (i.e., it takes longer from the time the Kanban signal is sent out until the completed product comes back).
Therefore, if you need a system that reacts quickly, it may be advisable to make the Kanban loops not too big. Smaller loops can react quicker to changing customer demand. This is especially important if you have many low-runner products that you don’t keep in stock and produce only as needed.
An interesting question here is the effect on the quantity of work in process (WIP). How is the WIP influenced by the number of Kanban loops? The longer the loop, the more Kanban you need to cover the replenishment time. A shorter Kanban loop has less replenishment time and hence less stock, but you need more loops. I did quite a few calculations on that and – in short – it doesn’t make much difference. Overall WIP does not change much if you make one big Kanban loop or multiple smaller Kanban loops. True, there are some differences, but it depends heavily on the system. For some systems there may be less WIP with one big loop, while other systems may have less WIP with multiple small loops.
10: Supermarket for Change of Responsibility

The final reason to opt for a supermarket instead of a FIFO lane is if there is a change in responsibility. If the material flow leaves one department and enters other departments, a supermarket may make things easier.
From the simple point of the material and information flow, this would not be a requirement; but whenever there are people involved, things are rarely simple. A supermarket to decouple the material flow can keep responsibilities more separate. This has nothing to do with hard facts but everything with things like “my turf” and “your fault.”
If there are FIFO lanes across department boundaries, there is a risk of the first department carelessly throwing things over the wall and the second department equally as carelessly throwing information back. Neither will help the overall operations of your plant. A decoupling using supermarkets can keep these systems more separate.
Again, from a purely logical point of view, this may not be necessary, but I have seen many plants where such blame games were a part of everyday life. Judge for yourself if this may be a factor worth considering with your plant.
In sum, in most cases it is possible to use both a supermarket or a FIFO lane. In general, a FIFO may be easier, but there are cases when a supermarket may be less trouble. I hope these guidelines helped you to decide between supermarkets and FIFO lanes. If, in your opinion, I missed a reason, please let me know.
Now go out and improve your industry!
PS: If you need an academic citation, you can check this paper. Please note that the numbering of the ten points is slightly different, but covers the same ground.
Roser, Christoph, and Masaru Nakano. “Guidelines for the Selection of FIFO Lanes and Supermarkets for Kanban-Based Pull Systems – When to Use a FIFO and When to Use a Supermarket.” In Proceedings of the International Conference on the Advances in Production Management System. Tokyo, Japan, 2015.
Hi, gone through this article on Fifo lanes and supermarket and find it very useful. If you can help, I have a different case at my factory. I am working at a cashew processing factory. If you have never known of this process then in short, its a single input and multiple output process. Like, we have raw cashew nut as single input raw material and towards the end of the process atleast 36 different products (grades as we call it) come out. Now, the problem is traceability, not having fifo, deteriorating product quality upon aging as there is no fifo in place and a lot of other issues. Pls let me know if you can be of any help in sorting out some of the issues.
Hi Raj, I like cashews and eat them a lot :). Although I have never been in a cashew factory. I assume there are some general processes at the beginning (cleaning), and then the nuts are sorted by size and quality. I can imagine that with continuous processes it is hard to tell where one batch ends and another one starts. You could leave a gap … but you would lose some capacity for machines running empty. You could add a marker of some sorts … but you would have to make sure that the customer does not get this marker in the package (risky). Maybe best would be to time the system based on conveyor belt speed to predict when the batches should be where. This of course works only if there is no “big bucket” or silo in between that mixes up the batches (in worst case in LIFO sequence). Hope this helps.
Should a FIFO be linked to the supplying process or the receiving process if there is a manageable but noteworthy physical distance between them? I am sure the answer is more detailed then either/or and it depends but I think this question maybe gets into the human factors of a supermarket being beneficial instead of a FIFO due to human factors around changes in responsibility. Thanks in advance for your time and answer.
Hi Ryland, long distance fifos are hard. In this case, a separate pull loop for logistics may be better.
Hi Christoph, thanks for the response. By separate pull loops are you suggesting a FIFO or supermarket tied to the supplying process as well as a FIFO/supermarket before the receiving process?
Hi Ryland, I am suggesting a transport kanban (if it is make to stock). Or just ship it if it is make to order. The FIFO will probably get a messed up, but that may be acceptable compared to the effort to maintain a long-distance FIFO sequence.