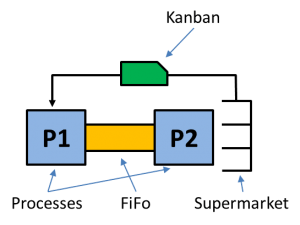
It is generally accepted knowledge that a lean manufacturing pull system uses both FIFO lanes and supermarkets to manage the material and information flow. However, there are few guidelines on when to use a supermarket and when to use a FIFO lane. This post is the first of a two-part series that will give ten general rules of thumb for when to use a supermarket instead of a FIFO lane. The second post will go into more detail about the ten rules.
In this first post, we’ll cover some of the basics. In short, you should use FIFO lanes whenever there is no reason for supermarkets. However, there is one hard rule when to use a supermarket and a number of situations when a supermarket may be better. These are all explained in much more detail my next post, but for the impatient reader, here is the list of the ten rules for supermarkets:
- Supermarket for process specific lot size differences (the only hard rule)
- Supermarket in front of the customer
- Supermarket if material flow splits up into different directions
- Supermarket between very different cycle times
- Supermarket between different shift patterns
- Supermarket when creating different variants
- Supermarket for merging of material flows
- Supermarket for large distance between processes
- Supermarket in the case of high demands on flexibility and reaction time
- Supermarket for change of responsibility
The Basics
Before we go into detail about what to use when, let’s just quickly review what a FIFO lanes and a supermarkets are, and how they combine into the information and material flow in a Kanban loop.
FIFO Lanes

FIFO stands for “First in – First Out.” The first part that goes in is the first part that goes out. There is no overtaking of parts. There is usually a limit to the number of parts in a FIFO lane. When the line is full, the previous process stops.
As such, production in a FIFO lane is very easy to manage. Only the first station needs to know what product to make. All other stations simply make the products they receive from the previous station. Overproduction is avoided through the limited capacity of the FIFO lane.
Supermarket
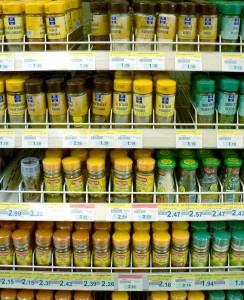
In manufacturing, a supermarket is a series of parallel FIFO lanes sorted by product. The name comes from the normal retail supermarket. The key of a supermarket (both retail and manufacturing) is that taking out any part or product gives a signal to replenish this part (a so-called Kanban). Hence, a supermarket also aims to keep all parts in stock, while at the same time avoiding overproduction. Compared to a FIFO lane, a supermarket takes more effort to set up and manage.
Information and Material Flow in a Kanban Loop
FIFO lanes and supermarkets can be combined with processes to create an information and material flow loop. The image below gives a simple example using symbols commonly used in industry.

The Question – When FIFO and When Supermarket?
Usually, good lean manufacturing systems are split into different information and material flow loops with a supermarket at the end. Hence, a good lean production system uses primarily FIFO lanes and supermarkets. The big question, however, is when do you use a supermarket and when do you use a FIFO lane. Below are four possibilities with three processes. You can make a big loop over all three processes, split the processes into two loops, or even split the processes into three separate loops with one loop for each process.

After covering these basics about supermarkets and FIFO lanes, my next post will go into more detail about when to use a FIFO and when to use a supermarket.
PS: If you need an academic citation, you can check this paper. Please note that the numbering of the ten points is slightly different, but covers the same ground.
Roser, Christoph, and Masaru Nakano. “Guidelines for the Selection of FIFO Lanes and Supermarkets for Kanban-Based Pull Systems – When to Use a FIFO and When to Use a Supermarket.” In Proceedings of the International Conference on the Advances in Production Management System. Tokyo, Japan, 2015.
Kindly help me understand the supermarket by using basic commodities in a diagram please. So i could be able to use it as reference to make and discuss my assignment. Thanks in advance for your favorable response.
Hi JoeReagan, have you seen my post Theory and Practice of Supermarkets – Part 1 and Theory and Practice of Supermarkets – Part 2?
Really interesting read so far about FIFO lanes and the supermarket. I like that you mentioned that a supermarket is like a bunch of FIFO lanes sorted by product. Kind of makes me interested to learn more about the history of supermarkets and how their designs changed over time.
Hi Taylor, if you are into the history of Lean, check out my blog post The History of Manufacturing – Part 4: Toyota and Lean or also my book Faster, Better, Cheaper 🙂
what about sizing the supermarket?
is it just demand + safety stock?
How do you figure out how much you need to carry if the processes have different cycle times? Would you just size it big enough so that the downstream process empties the supermarket on Friday and the bottleneck process works weekends to refill it for Monday?
Hi Michael, that would be the kanban formula.
Use the kanban formula K=D*LT+ SS
K= kanban quantity
D= average daily consumption (demand)
LT= lead time in number of days to replanish
SS= safety stock (depends form many factors. Variance of the demand could help to estimate SS