

Modern workplace management undoubtedly started with Frederick Winslow Taylor (1856–1915), who almost single-handedly created modern industrial management. He was the first to measure industrial work and apply the results to improve efficiency. Even so, efficiency was greatly improved by Frank and Lillian Gilbreth (1868–1924 and 1878–1972 respectively). Unfortunately, Frederick Taylor and Frank Gilbreth were at war with each other. This post looks into the history of how the conflict started, and how Lillian Gilbreth resolved the conflict after their deaths.
Frederick Winslow Taylor
Frederick Taylor is considered to be the father of modern management science. While it was intended for him to study law at Harvard, he instead became a machinist. Starting on the shop floor, he established the entire field of scientific management, often named after him as “Taylorism.”
His most famous showcase project was the optimization of workers loading pig iron onto carts at the Bethlehem Steel Company. Through his methods he increased the loading of iron from 12 ton per day to 47 ton per day – albeit modern research showed that he was definitely fudging his numbers there.
In any case, he established the entire field of scientific management by measuring work and trying to improve efficiency.
Frank Bunker Gilbreth
Like Taylor, Gilbreth started out by working with his hands, in this case as a bricklayer. He started to optimize bricklaying methods, significantly improving the speed of bricklaying, and found himself soon working as a consultant in the field of Taylorism.
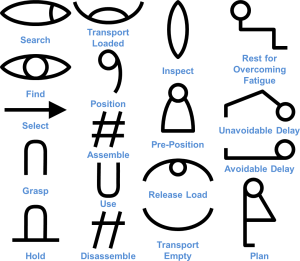
His major contribution was to divide all human work up into a number of individual motions, which he called Therbligs, and then optimize these motions to improve efficiency. For example, with bricklaying he created an adjustable scaffold so that the bricks, the worker, and the wall are always at the same height, and hence the worker does not have to bend over or reach up.
He also optimized surgeons’ work, establishing the now-common method of a nurse handing the instruments to the surgeon rather than the surgeon turning around and looking for the right tool. By reducing the duration of operations, he increased the chances of patient survival, saved thousands of lives, and pissed off the surgeons after they found out that he used the same methods for bricklayers. Surely those holier-than-thou doctors deserved better than to be compared to a bricklayer. 😉
Overall, his work was the basis for any system of predetermined motions in use nowadays. His work was also a perfect addition to Taylorism.
The Conflict
Taylor was good at optimizing work. But even more than that, he was stubborn. Anybody who wanted to work with Taylor had to agree with him or be prepared for an endless fight – and it didn’t matter who paid who’s salary. Taylor would not hesitate to fight his employers and clients over the right way to do things.
As such, he quarreled with many other researchers. He did initially give Gilbreth credit for his work, but he soon started to quarrel with him too. Taylor considered his methods unsuitable. After Taylor’s death, his Taylor society even kicked it up a notch, and Gilbreth found himself under constant academic fire from the much stronger Taylor society. They took the approach from Gilbreth – thank you very much – but attributed it to their own society while at the same time trashing Gilbreth.
While Taylor had established a large society of followers, Gilbreth was working only with a small group. Hence, after Gilbreth died, it looked like the Taylor society has won. However, there was one woman who made a difference!
Lillian Moller Gilbreth

Lillian Gilbreth was a power-woman. She not only studied at university – a rarity for women around 1900 – but even got a Ph.D. in psychology. She also significantly contributed to her husband’s research and was one of the first female engineers and the first industrial psychologist. For example, she significantly contributed to the layout of the modern kitchen. Previously, a kitchen had a working table in the center, with shelves on the walls. Hence, women (and it was mostly women in the kitchen in 1920) had to turn around every time they needed something. Lillian Gilbreth established the modern kitchen layout with workspace around the walls, and shelves for tools and ingredients above and below.
She also gave birth to twelve children, eleven of whom reached adulthood. If you’ve ever had a child, you definitely appreciate the work necessary to raise eleven of them! But then, she and her husband also used their skills in organizational efficiency in the upbringing of their kids (if you want to know more, there is a great book, Cheaper by the Dozen, which was also made into a film in 1950).
After the death of her husband, she managed to promote her husband’s work, consult these methods in industry, and make peace with the Taylor society. Not only did the Taylor society end the conflict, they even acknowledged the contributions of the Gilbreths and praised their work. It is mainly due to her work that the name Gilbreth is now recognized as a major contributor to modern workplace efficiency.
PS: If you would like to read more about history of manufacturing, then check out my book:
Roser, Christoph, 2016. “Faster, Better, Cheaper” in the History of Manufacturing: From the Stone Age to Lean Manufacturing and Beyond, 439 pages, 1st ed. Productivity Press.
Brilliant and enjoyable website. Thanks
So glad to see Lillian and Frank Gilbreth, my favorite couple, get some notice. I consider them to be as Lean as they come. Thank you for featuring them.
They were amazing. I am sure you read “Cheaper by the dozen”, with lots of funky details on their family. I also consider Lilian to be a real power woman, most impressive! I definitely like them more than Taylor, which often manipulated the truth to his liking and did not accept compromises.
As a young work-study engineer and rate-fixer in the 1960’s, my main sources of information was not Taylor’s original material, but all my trainers and the authors of my study material referred to Taylor and the Galbreth’s as the original source for ‘Scientific Thinking’ and ‘Time and Motion Study’. I cannot have been alone in finding this material inspiring. When I move into the metal cutting industry, I used Taylor’s tool life equation and its expanded form, as an essential tool for analysing tooling performance and metal cutting economics.—
A point often missed about Taylor was his visionary abilities. This is best explained in his own words. In 1912 he was called before a Senate committee to explain his system for improving productivity. Some years ago the BBC broadcast a radio programme about Taylor and the effect of his teachings called, ‘The time and motion man’. Part of it included dialogue based upon transcripts from this investigation. I recorded it at the time and the comments below I documented. —
Chairman Wilson.. “What is the economic necessity for increasing production?”
Taylor. “The world suffers now, as it always has from underproduction. Underproduction is responsible for low wages, and the reason the poor have fewer things in terms of the basics and luxuries to live on. Have poorer food to eat, pay higher rents and can afford fewer clothes. The only way to bring these things into the world is to increase output. Scientific management is about increasing the output of the man without increasing his effort. I firmly believe in the next 100 years the wealth of the world will grow to such an extent that the workman of the day will live almost as well as the high class businessman lives now; both as the necessities and luxuries of life”. —
I will leave the final word to someone we all admire; and is considered by many to be the father of modern management.
“In 1881, an American, Frederick Winslow Taylor (1856-1915), first applied knowledge to the study of work, the analysis of work, and the engineering of work. Darwin, Marx, Freud form the trinity often cited as the’ makers of the modern world’. Marx would be taken out and replaced by Taylor if there were any justice in the world. But that Taylor is not given his due is a minor matter. It is a serious matter that far too few people realise that the application of knowledge to work created developed economies by setting off the productivity explosion of the last hundred years.” Peter Drucker.
On my first few visit to Japan to study the Toyota Production System, I quickly appreciated that they had developed their own form of ‘Scientific Management Thinking’. The main difference to the Taylor model was that they had engaged all their people positively in the process.
Let us hope our present improvement methodologies have as much impact on human prosperity in the next one hundred and thirty years, as those of Taylor and the Gilbreth’s have done over the last one hundred and thirty.
Hi Sid, thanks for the long comment. You should definitely also check out my post “100th Anniversary of the Death of Frederick Winslow Taylor, the Father of Modern Scientific Management“. Taylor was indeed quite a character, with strong good and bad sides!