Continuously moving assembly lines have a lot in common with other types of assembly lines. However, there are also some differences. This third post of this small series on continuously moving assembly lines looks at how to distribute the work along the line. The key point is that you can distribute the work along the line in proportion to its duration, but the worker and the machines have to follow the takt time. Let me explain.
A Quick Recap
The work that has to be done on the continuously moving assembly line could simply be distributed along the line in proportion to the duration of the work. Together with the line length this will determine the line takt. If the line takt does not match the customer takt, then you can either change the work content or change the line length.
Workers Follow Takt
The workers, however, need to follow the takt time. Below are three scenarios that similarly apply if a robot or a machine is doing the processing.
- If the work content for a worker is less than a full takt time, then it is perfectly fine to assign only the required space to the assembly line. Afterwards, the part moves into the next station. The worker will also be able to do his work and then move to the beginning of the assigned space. However, when the worker arrives at the beginning, the next part has not yet arrived (since it is exactly one part per takt), and the worker has to wait. If you assign less work than one takt to the worker/station, you don’t need as much line length but waste the workers time.
- If the work content for a worker is just about one full takt time, then you have the best case scenario. The space on the line is long enough for one takt, before the part moves into the next station. The worker also can do his work. When the worker then returns to the beginning of the assigned space, the next part is just arriving and he can work continuously. If the assigned work matches the customer takt, then the time of the worker is not wasted.
- If the work content for a worker is more than a full takt time, then the space on the line has to be extended accordingly to match the time. This way the part is available for the station for the extended time. The worker can complete the first part, but since this takes more than one takt, the next part is already within the work station when the worker completes the first part. The worker is then delayed with starting the next part, and will not be able to complete the task on time. You would need more workers to complete the work. If the assigned work exceeds the customer takt, then the worker cannot keep up and the line will slow down or stop (more on this later).
Work Content Exceeding One Takt
Let’s go into more detail on work content that exceeds one takt. We already saw that this either requires additional workers or it will slow down and stop the line. You need to provide additional capacity to complete the work. Below is an example from conventional line balancing. You simply increase the number of identical, parallel work stations. The example below is balanced to two takt times (or cycle times if you calculate without losses), and two stations can handle the work. Similarly you can use three or more stations for work content of three or more cycle times. This works best if the work content is a whole integer multiple of a takt time. In other words, two stations for twice as long, three stations for a work content that requires three takts, and so on. It creates waste if it includes a fraction of a takt (i.e., if you have 2.5 takts worth of work content, then you still need three stations, wasting half a takt worth of work with every part).
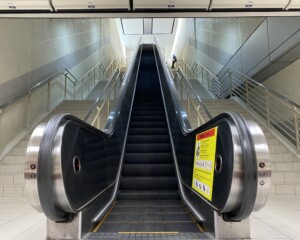
For a continuously moving assembly line, however, it is not possible to split the line into two for one station and merge them again. But there is an elegant workaround. You simply have two or more stations in sequence. You could have one worker at each station handing over a half-finished part to the next, albeit I imagine that the handover is tricky. It may be better to have two (or more) workers on a longer station. Below is an example with work content for two takts. Two workers handle this station together, being one takt of time apart from each other. The first worker takes the part and starts working. The second worker takes the next part one takt later. By the third takt, the first worker is done and has returned to the start of the station to handle the third part.
Similar applies to work content that is three, four, or even more takt times long; you simply use three, four, or more workers in a loop. The walking distance also makes not much difference. A single worker walks back one station every takt, two workers walk back two stations every two takts, hence, similar walking times per time. It may be a bit trickier for machines or robots. While you still need multiple robots for a multiple of a single takt, moving the robots or machines back to the beginning while another robot or machine moves in the opposite direction is tricky.
Also, be aware that the line has to be long enough to fit all the workers, machines, and materials along the line.
Please be aware that this still works best if the work content is as closely as possible a whole integer multiple of one takt. If it is not, you again introduce waiting times (or line stops), even though the space on the line can match the work content exactly. In sum, whenever you have workers or machines, you still have to do a proper line balancing, even on a continuously moving assembly line, or you will introduce waste in the form of waiting times (work less than takt) or line slowdowns and stops (work more than takt). In my next post I will discuss the (admittedly) uncommon situations where the part needs time, but no worker or machine. Now, go out, balance your line (continuously moving or not), and organize your industry!
PS: This series of blog post was inspired by Sobha Modular.