Normally, assembly lines are run with a product in every slot of the line. However, for various reasons, sometimes you may have an empty spot. Depending on your assembly line, you may even play with the general distance between products on the line. The latter is called variable takt, or VarioTakt. In this post I will explain about empty slots on the assembly line, and in the next post I will explain VarioTakt in more detail.
Introduction
Many assembly lines, by design, move products at fixed intervals. This is usually some type of workpiece carrier, where the product is on a carrier or hanging from an overhead position. Hence, for every position you have a binary option of having a part… or not having a part. An assembly line could be fully occupied with a part in every slot, or there may be gaps between parts. (Having an empty line with only a few parts running is unusual except for a ramp-up.) The image below visualizes such gaps on assembly lines with fixed intervals.
Unplanned Gaps
The normal way of operation is to have an assembly line full with parts. Every slot has a part, and the line runs at full capacity with full speed. This is often the most efficient way to run an assembly line, as every station is working on a part at every interval, regardless whether it is a pulsed line where all parts move once per takt, or a continuously moving assembly line where the parts move all the time without stopping (except for abnormalities).
In such a situation, any gaps are unplanned. A product may be defective or missing a crucial part, and the decision has been made to no longer work on the product. In some cases the product is removed from the assembly line; in others it stays on but it is no longer worked on. The effect is the same: every station on the line after the decision was made has an idle takt, where the workers have one takt of time but do not work on the defective product (either by instruction or if the product has been removed). The entire line loses one cycle of efficiency after the decision not to make the product.
Planned Gaps—Changeover
However, there are also planned gaps in the line. One such example is during a running changeover. When the last lot of the old product is completed, you leave a number of slots empty for the changeover before adding parts of the next product type on the line. The number of empty slots should correspond to the number of takt times that you need to do the changeover. In other words, if your line normally produces a part every minute, but the longest changeover for one station needs up to three minutes, you should have a gap of three parts (i.e., three takt times i.e. three minutes) for the stations to do their changeover.
This time for a changeover applies to all stations. In other words, if you have a gap of three minutes, all stations have three minutes of time to do a changeover, regardless whether they need it or not. If a station has a faster changeover, or no changeover at all, they receive up to three minutes of idle time in this example. Hence, an unequal duration for changeovers at the different stations leads to losses. Fortunately, you usually have relatively few changeovers compared to production time, so the losses are small. Or, you could just eliminate the changeovers altogether (see SMED) and avoid the problem completely. This would also allow you a lot size of one. Theoretically this could also apply to maintenance, but I have not seen this, and maintenance is usually done on off-shifts when the line is idle anyway. See also below for an animation of a running changeover with a changeover duration of one takt.
Planned Gaps—Low Demand
Another reason to have gaps is in case of low demand. The customer needs less than the full capacity of the assembly line. Or (worse), your supplier provides fewer parts than needed for the full capacity of the assembly line. In this case, too, you COULD have gaps on your assembly line. However, you are opening a whole can of worms that are not easily managed!
If you keep gaps in the assembly line, you have to decide what to do with the workers at the station. If you just leave them there, then all stations have idle time corresponding to the number of gaps. In this case it is usually MUCH more efficient to run the line at full capacity and turn it off completely when you have reached the limits of your demand (or your supply). Afterward you could send your workers home or assign them to other lines or stations.
If you still want to use gaps, you either have to live with the idle time or find a way to use the time of your workers for other (more or less) value-adding activities. This is possible, but it becomes trickier as the takt times become shorter. If you have a gap on a line with a takt of one minute, it is hard to reschedule the workers for one minute and then have them come back to the assembly line. At best they could do some other activities like cleaning or collecting trash.
However, as your takt time goes up, the effort to manage the time of the workers becomes easier. A one-minute gap is hard to use. A one-hour gap can be used much easier. The one example I know is the final assembly line of Trumpf, where the laser tools are made in a takt of one shift. Re-planning your workers for a different task for an entire shift should be quite doable. Their assembly line is shown below.
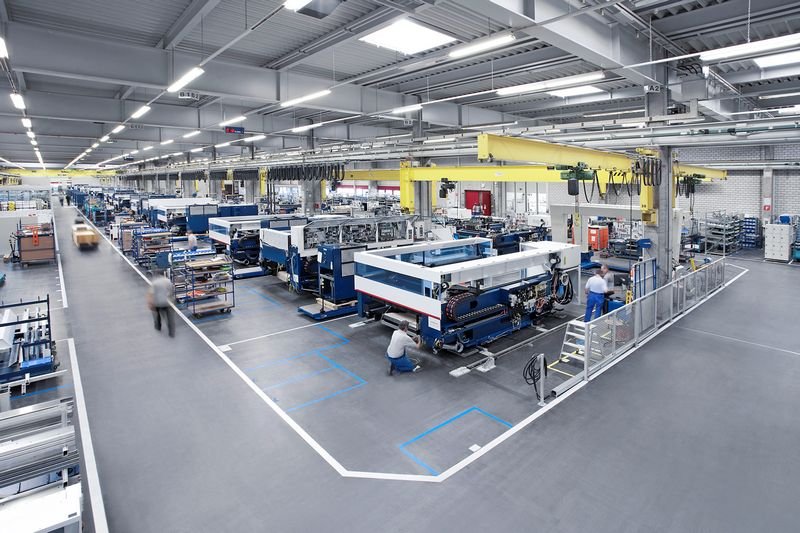
Planned Gaps—Fluctuation in Cycle Time
Another possible reason to have gaps on the assembly line is if your products have different workloads. You may have small and easy products that are worked on quickly, but also large and tricky products that require more time. A gap in the assembly line could give such a more-time-consuming product more time, as illustrated below.
Fixed Interval vs. Variable Interval
You can leave one piece empty and create a gap in the sequence of products on your assembly line. This is done sometimes, but on fixed assembly lines there is the limitation that the gap always has to be one part (or a multiple thereof). Hence, you can provide additional time for more time-consuming parts only at intervals of one takt time. Such lines usually have workpiece carriers or hanging carriers at fixed intervals.
However, some assembly lines do not require fixed intervals between parts. The easiest example is a simple conveyor belt or rolling lane, where you can place your products anywhere on the line. Similarly, AGV (automated guided vehicles) can also be flexible regarding the distance between products. Below is an example of a fixed interval assembly line with a one-piece gap, and a conveyor belt and an AGV system with a gap of half of a piece and hence half of a takt… but it could be almost any number larger than zero.
However, all stations will get an extra takt for this high workload product. Yet, chances are that only a few stations actually need this extra time. Now we have again the problem of workers on stations having (part of) an idle takt that wastes their time. And, with only the option of an empty slot, you have only the option for an integer multiple of takt times to play with. You cannot give the part “half a takt” of extra time… at least not if you use such workpiece carriers at fixed intervals. However, there are options if you can have parts on the assembly line at fixed intervals. This variable takt is used by the German agricultural machinery manufacturer Fendt. I recently had the chance to visit their plant and also talk with the inventor of the variable takt, Mr. Peter Bebersdorf. In my view, Fendt is a benchmark on handling variability on an assembly line. But more on this on my next post. Now, go out, look at possible gaps in your assembly line, and organize your industry!