This post continues to discuss running a plant in a war zone. While the first post focuses on the difficult question of whether you should continue operations, this post looks at what you could do if you decided to continue running your plant despite the armed conflict nearby.
Stay and Keep Working?
If the decision of the plant is to keep operations running (for now), there are many additional problems to consider. War will disrupt your supply chains, and if you thought you had a bad case of missing parts before, it will look like child’s play in comparison with the disruptions you may be facing.
The disruptions in the supply chains are similar to disruptions in peacetime, just larger. You can use similar approaches to deal with them, although due to the size of the disruptions, chances are higher that sometimes it won’t work out and operations will stop due to a lack of material.
Like any fluctuation in the material flow, it can be decoupled through inventory, capacity, or time. Plants in a war zone may increase inventory to cover fluctuations. Adjusting or increasing capacity may be difficult. In reality, the most common fallback decoupling will be time, and your customers may have to wait for their goods. Inform them about your situation, and ask them for their understanding.
But overall, the fluctuations in the material flow and its countermeasures are similar to peacetime, except you are playing on hard mode. However, the risk of employees getting hurt and your equipment and property getting damaged by far exceeds peacetime expectations.
Safety of People
Safety should always be a concern for anybody working in industry. During an armed conflict, it may not be possible to guarantee a peacetime level of safety. Nevertheless, steps can be taken to reduce the risk to your people. It should start with a risk assessment. What kind of additional dangers are your employees (and also your equipment) exposed to due to the armed conflict. Is there a risk of a missile attack or an air raid? Could enemy troops cross the area? Is your plant maybe even an special target of interest to the enemy? Is there a risk of nuclear, biological, or chemical attacks? Depending on this assessment you can consider steps before, during, and after an attack.
Before the attack you should prepare your people and your plant. If you expect air raids, do you have bomb shelters nearby? Do you need to prepare shelters? Anything from a sand-bagged location to a sturdy and safe basement could do. If a bomb goes off nearby, glass windows are especially dangerous and could turn into deadly shrapnel. While explosion-resistant windows may not be an option, please consider possibilities. During World War II, duct tape was used across windows, although this may make it even worse with larger shards and may not be advised. Putting plywood over the windows may be a better solution.
Plywood could also help to black out the plant. During WW II entire towns blacked out light, although modern military targeting may not make this necessary. You should also consider fire hazards. Can you reduce these hazards? Can you move the flammable items farther away from the plant?
Also important is to make sure you have enough easy-to-reach first aid equipment, and it is well stocked especially in view of wartime injuries. Similarly for fire extinguishing gear, from buckets of sand to proper extinguishers. Are your people trained in how to use this gear?
During an attack it is important that your people react quickly. An air raid warning may be a few minutes before the actual attack. Make a plan if there are some machines that need to be turned off (quickly), and practice heading for the nearest shelter.
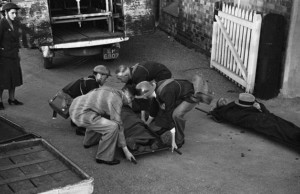
After the attack you may need to treat the injured and fight fires. Are you lucky and your people escape with only minor injuries? Do you need an ambulance? Are there fires? Your people (and maybe also you) may be at least shaken and disturbed. What can you do for mental health? And, not the most important first part but eventually also necessary, you should resume operations.
Safety of Your Equipment
Besides your people, you also may want to protect critical equipment. You could put sandbags around your important machines to reduce possible damage. Some actions that protect your people (plywood on windows, reducing fire hazards) may also protect your machines.
Safety of Your Knowledge
Finally, you need to protect the institutional knowledge of your company. The experience of your employees is protected by protecting your employees. But do not forget to make backups of your data! Preferably on a server far away from the war zone, or even in a different county. If you store your backups in the same room as your server, both may be destroyed and you will be left without the data. Actually, this advice applies to anybody everywhere. Backup your important data!
In any case, I hope this post was interesting to you. I hope even more that you don’t ever need this post. Now, go out, backup your data, and organize your industry!
PS: I wanted to write something in support of Ukraine and fitting the theme of this blog for quite some time now. Many thanks to fellow LGN member Serhii Komberianov from the Lean Institute Ukraine for giving me the inspiration!
Hmmm! I’m not sure how relevant all of this is to the usual stuff, although I understand your motives. A couple of -maybe also irrelevant- points:
– in the early days of WWII, the RAF used small bombs on factories. They didn’t seek to blow equipment to smithereens, just wreck the roof and let the weather do the damage
– German aircraft manufacture reached its peak in 1944, when Allied bombing had also reached a peak. Sourcing aircrew and fuel was a different matter….
– around 1992 I visited a paint factory in Sheffield. The floor was very bumpy, and paint was carried around in large open-topped tanks which inevitably sloshed around, spilled onto the floor and made it bumpier when it dried. This had been going on for 50 years since the Luftwaffe bombed it! They’d holed the roof and spoiled the floor …a pity they’d not used incendiary bombs and forced the company to make a fresh start!
Hello, I think you make some great points which I tried to summarize below:
War will disrupt supply chains
– Similar to those in peacetime, just larger
– Risks are greater
– One of the biggest disruptions might be time, so make sure you clearly communicate your situation to customers
Risk assessment – this analysis will help with potential solutions
Train employees in emergency scenarios as form of mitigation
Don’t forget about the mental health effects of these attacks
Protect institutional knowledge of company –> have backups of data
Although I think some of the examples you give may be somewhat obsolete with war related technological advancements, I think the underlying concepts can still be applicable. I believe they can even be applicable to non war-time scenarios too such as clearly communicating with customers your given situation and, like you mentioned, having backups of crucial data.