This is the third and last post in my series on how to reduce the lot size. The first post gave some introduction and how to approach the problem of reducing lot sizes. The second post looked in more detail at how to reduce lot sizes due to changeovers, container size, and shipment size. This final post will look at the remaining causes of customer order size, machine batch size, the abominable leveling pattern, and tradition.
Reduce Lot Sizes Caused by Customer Order Size
Another possible reason for your lot size is your customer order. If the customer orders 300 pieces, then of course he will get 300 pieces. Yet, you still can make smaller lot sizes. There are two basic directions in which you can reduce lot sizes. You can do this independently from the customer order. If the customer orders 300 pieces, then you can make once 300 pieces, or three times 100 pieces. At this point, accounting will get high blood pressure again, since 300 pieces once is more efficient than three times 100 pieces…or at least that is what their numbers tell them. However, it is again a case where the cost can be measured but the benefit is hard to put in numbers. Please do consider smaller lot sizes even if there is a larger customer order.
Just reducing the lot size internally despite a larger customer order does give you the benefit of less inventory and reduced fluctuations. Unfortunately, to the customer side you still have the large order, and hence lose out on these benefits. However, this can be changed too, but now you have to work with your customer. Can you convince the customer that three shipments of 100 pieces each is better for him too, rather than one shipment for 300 pieces? You may run into the same arguments from accounting (again), arguing the cost and ignoring the hard to measure benefits. I know examples, however, where the customer was open for such suggestions, and also benefited from the reduced lot size.
Reduce Lot Size Caused by Machine Batch Size
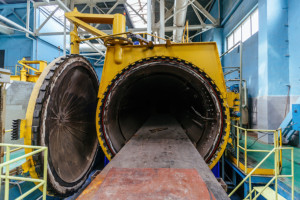
Many machines process parts one by one. However, some processes can treat multiple parts at once. For example, an oven can harden multiple parts at the same time. A flash freezer freezes multiple products. In the processing industry, the batch size (i.e., lot size) is pretty much how much you can fit in the pot. The solution to smaller lot size initially also sounds obvious, just put less parts in the oven/freezer/pot/whatever.
Unfortunately, here we may often find issues with the process parameters. The number of items in the process can influence the process parameters and/or the quality of the product. If the oven has many parts, it may need different temperature and time settings than if an oven has only a few parts. It can be done, but make sure that quality does not suffer.
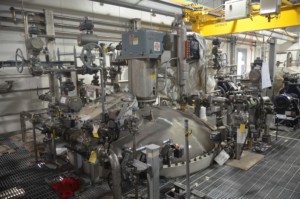
This approach also has a comparatively large impact on capacity. If you, for example, half the lot size due to changeovers, you double the changeovers. However, changeovers are only a small part of the overall time, and if you initially lose 5% due to changeovers, you now lose 10% of the time. This is unfortunately different with an oven. If you fill the oven only to half capacity, you use only half of the capacity (or maybe a smidgen less due to faster heating times). hence, halving your lot size also halves your capacity, and this is not always a feasible way. Additionally, if you need slightly more capacity due to more frequent change overs, a SMED workshop can help to reduce the changeover times again. For your oven, however, it is usually not possible to significantly reduce the time needed for a batch. If you roast two chickens in an oven at 180°C for 1 hour, then one chicken will still take about 1 hour. Doubling the temperature to 360°C while reducing the time to 30 minutes will NOT give you the desired results. Hence, unlike SMED, it is really hard to reduce the processing times for such batch processes.
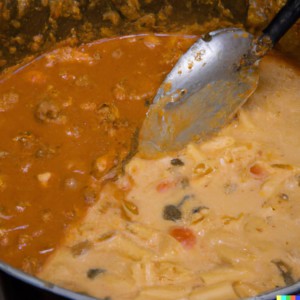
It is also not always possible to mix and match different products in the same batch. If you roast a chicken and a turkey in the same oven at the same time, you may be disappointed by the overcooked chicken and raw turkey. Similarly, in the processing industry you cannot whip up half a batch of sauce Bolognese and half a batch of Alfredo sauce in the same pot.
Overall, if your lot size is due to the machine batch size, your options are limited. The only feasible way requires significant investment by replacing one large batch process by two smaller batch processes. Or, even better, when a new system is set up, two smaller batch processes are installed from the start instead of two larger ones. But this, again, will raise the blood pressure of accounting when they calculate the cost. However, it can be done, and has been done. It just may not be cheap.
Reduce Lot Size Caused by Leveling Pattern
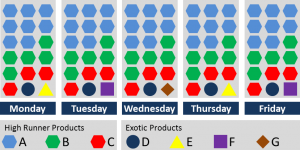
Another reason for lot size is a leveling pattern. Leveling, in general, aims to reduce fluctuations. However, there is one type of leveling that does this not very well, and which in my experience in general does not even work. This is a multi-week leveling pattern, where there is a single batch for every product every day (or every shift) based on the average demand for the next few weeks (often 1 to 4 weeks). Hence, your lot size is your expected average daily demand, at least for the high runners.
One possible solution is to make the batches smaller. You can take the average demand for half a day, or the average demand for two hours. Or, possibly better, you define a smallest feasible lot size, and break the demand down to chunks of this lot size. Compare for example the improved pattern here with the previous pattern.
I have written on The Folly of EPEI Leveling in more detail, because it almost never works. Most companies cannot reliably produce tomorrow what they decided yesterday. A multi-week pattern is bound to fail and to increase chaos. Hence, my most preferred solution to reduce your lot size due to your leveling pattern is don’t use a multi-week leveling pattern!
Reduce Lot Size Caused by Tradition
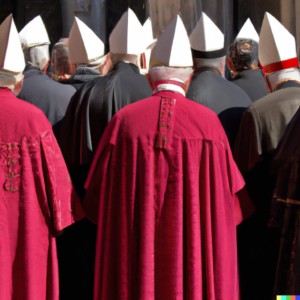
A lot size that is based on tradition may be simultaneously the easiest and the hardest lot size to change. It may be the easiest, since there is no real reason for this lot size, and reducing the lot size can be done with the stroke of a pen.
At the same time it may be the hardest, because it is tradition, and the people may oppose the change because of tradition. Depending on which situation you find in your plant, you may have to do a lot of talking and convincing to get your people on board.
This concludes this small three post series on how to reduce lot sizes. Now, go out, fight tradition (or whatever restricts your lot size), reduce your lot size, and organize your industry!
Hello Christopher, I enjoyed reading your post about reducing lot sizes. I liked how you went into detail about the positives and negatives of reducing lot size caused by machine batch size. You mentioned that in your experience, a multi-week leveling pattern does not work at all and that they are bound to fail and increase the chaos. Do you have any specific examples of this happening in your experiences?
Hi Jason, when I worked in German industry, a multi-week leveling pattern was all the rage, and I have seen many tries. None of them worked. One plant was recommended to me by the former head of production for its leveling, but when I called the section deputies in charge of the different production areas as well as the head of lean, they all told me that it does not work. At a different time I had a discussion with the person in charge of leveling for a large worldwide car supplier with 100’s of plants and asked him where to go to see a good leveling, he just laughed at me and never answered my question.
The reality is, a lot of transportation and batch processes have a cost that’s mostly fixed and doesn’t change that much based on utilization.
A simple example would be a laundry washer and dryer. It costs MORE to load the machines half full and wash twice as many loads.
Another example would be passenger airlines. A completely empty airplane costs only 20% or so to fly than the plane loaded to the maximum takeoff weight. That’s why airlines oversell flights and eat the cost of paying an occasional passenger(s) who must be bumped to make the weight rather than flying half full planes.
Same thing with changeovers. changeovers are expensive in terms of time, and there’s usually no way to significantly reduce them (unless you’re building a new plant from scratch). Although many times there’s a way to rearrange customer orders to reduce the number of changeovers without too much delay in the lead times.
Andrey, I disagree. There are usually lots of ways to reduce the changeover time, and 30% is usually possible even without major invest (but minor stuff like a sensor or a jig etc). While maximizing the batch size reduces changeover time and saves money, the money lost due to the larger batch sizes is usually significant but underestimated, and sometimes even not possible to measure using cost accounting.