To become lean, you need to improve your factory. Continuous improvement (kaizen) consists of many smaller and/or larger improvements. However, often the first challenge is where to start this improvement. Let me dig deeper into the possibilities and challenges of picking improvement projects, with a particular focus on systems that have multiple independent production lines, which makes everything trickier.
Introduction
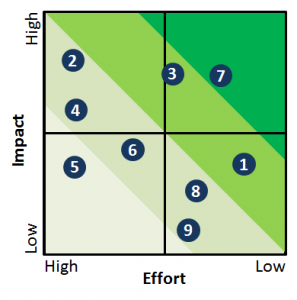
I have written about managing lean projects before. I find it very important to limit the number of active projects to something manageable, especially for the critical capacity (i.e., the shop floor manager) who has to be involved in them all. If you have a number of possible projects, an impact-effort matrix is often a good way to narrow it down and select a manageable number.
But this sometimes leaves the problem of picking good candidates for improvement projects. In this post I will show you a few ways to find improvement projects for consideration.
Your Boss
The easiest way to find out what to do is to simply ask your boss. He may just tell you what you have to do. However, this is a flawed approach (even though some bosses like it a lot). It rests on the underlying assumption that The Boss Knows Best … or Does He? In reality, however, bosses are so far away from the shop floor that they do not have a good understanding of the shop floor. Even if they are closer to the shop floor (good!) the people on the shop floor may be better informed. The exception is of course a new employee who does not know or understand the shop floor yet.
Luckily, better bosses won’t just tell you what to do, but involve you in the decision-making. Better bosses tap your knowledge to get a better result from your work. However, they should not leave everything to you. Just saying “do whatever you want” is not good either.
Ideally, the boss gives you a direction, sometimes with more and sometimes with less guidance, but always with support. This brings me to my next section.
The Overall Direction
In lean, it is really helpful to work in the same direction of improvement over a longer period of time. This direction could be managed by a Hoshin Kanri. While details differ from company to company, it is usually a variation or selection of cost, quality, time, and safety. Here, too, if you want to improve it all, you may not get good improvement in any of those areas. Which one is truly most important area in need at your company? And “all of the above” is not really a valid answer, as this merely means everything is equally unimportant…
Single Material Flow
If your priority is cost, time, or quality, then you should follow the value stream looking for waste, unevenness, and overburden (don’t forget the last two). What areas in the value stream give you problems in your selected area for improvement? (If it is safety, work on the accident-prone areas).
Finding improvements for cost, time, or quality is easiest in a single value stream. If all (or most) of your value add goes through a single final line in your system, then you can just follow the line backwards looking for problems. The image below shows the Toyota Motomachi line, and while the line looks complicated, it is all a single merging value stream. Only a small fraction of the value add of the plant does not go through this single dominant line (for example, spare parts).
Multiple Material Flows
Often, a plant has this single dominant line. However, many plants have multiple lines, and it may not always be clear where to start with kaizen. One example I visited recently had a whopping fifty different value streams, where each line attributes for roughly 2% of the value add of the plant (visualized below). These value streams making plastic parts were usually two injection molding machines in sequence with some additional processing and logistics in between. While there was some flexibility, most products could be produced only on one or two lines.
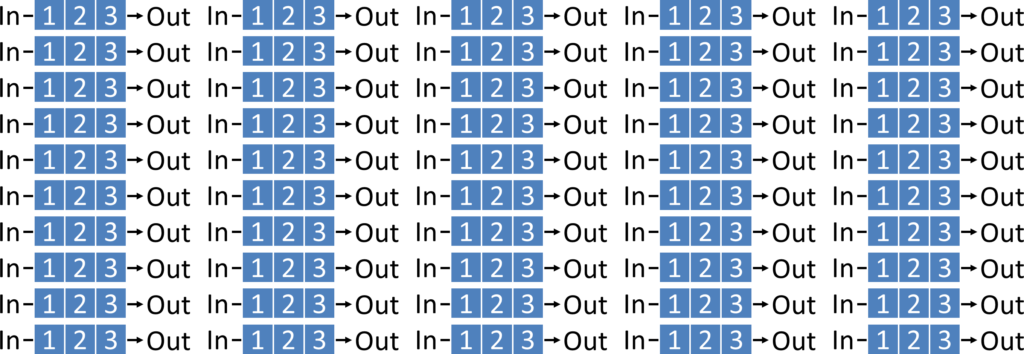
Here it is much trickier to decide where to do improvements. First, it is hard to decide which line to start with. All of the lines will have waste, fluctuations, and overburden. But which one is the most important one? Secondly, no matter which line you start to work on, it will influence only roughly 2% of the value add of the company. Instead of having one large and powerful lever like the single line-plant further above, you now have a multitude of smaller levers. Whereas the single value stream is a chain with a weakest link (quality, cost, time), now you have fifty chains, each again with a weakest link.
Now, the worst thing you could do is not do anything. While by not doing anything you don’t do anything wrong, you also do not improve either, and instead things will gradually get worse. You can worry a bit about which lever of the fifty is most beneficial, but at one point you have to invest time and money to pull this lever. And, chances are, there may have been another lever that was more significant, and you missed it. That is life, but it is better to do a smaller improvement than to do none at all.
A large lever in a plant with a single line is often large because the lever has many beneficial side effects along the line. It is also benefiting the majority of the products. An improvement in plant with multiple smaller lines will have much less beneficial side effects, and also affect a much smaller part of the products … while still having potentially the same cost and effort! You get much less bang for your buck, or for your efforts and time. The exception would be logistics, because improving logistics may improve the entire plant, even if it has multiple smaller and independent value streams.
As for finding relevant lines with good improvements, try to do your best to estimate the impact and the effort. If your target is quality, find out which products have the most frequent or most costly defects, and look at the lines producing them. Similarly for time, find out which products are often out of stock (for make-to-stock [MTS]) or have a bad delivery performance (for make-to-order [MTO]). If cost is your issue, look for products where your produced value is larger. Find possible improvements, compare them with the estimated effort, and pick the most promising ones, even though the underlying data is wobbly or fuzzy. Not doing anything would be the worst.
On a side note, small improvements that are little to no effort can be done regardless. If the workers want a better shovel to handle small parts, or if a tool is worn out, just fix the issue. At Toyota, small improvements are done anyway, without any cost and benefit analysis. Now, go out, improve your value streams, and organize your industry!
P.S.: Many thanks to Jonathan Folberth for the discussion that sparked this blog post.
Very informative thanks. Kindly give information how to reduce Truck Turn Around time-TAT
Hello Sayten, in general look for the major time blocks, and try to reduce them. Also look for fluctuations, as they are often much worse than the mean.
you have mentioned regarding how Toyota handles small improvements naturally and can you also refer or share an article regarding how to create such culture in different industry ? many thanks..
Hello Mustafa, I have no such article yet, but it is on my to do list to write about different scales of improvement projects.
Thanks for sharing.
I am working on my first six sigma green belt project, so I wanted to read this article to learn more about Kaizen and where to start your continuous improvement. Figuring out what needs to be improved can be very tricky and this article helped give me great ideas. The impact – effort matrix is a great tool to help identify which problem will be easiest and most effective to tackle. The article also highlights how by focusing on one specific area you are more likely to fix the problems. You need to determine whether your project should focus on saving cost, quality, time, or safety. This article also provided many good suggestions such as: finding out which products have the most frequent or most costly defects to improve quality and finding out which products are often out of stock to improve time.